Is Your Rigging at Risk? Experts Reveal Critical Inspection Tips
Industry Veterans Unveil Keys to Rigging Safety: Qualified Inspections and Third-Party Evaluations Are Essential for Compliance and Preventing Failures
Consistent rigging inspections identify damaged equipment before failures occur, preventing accidents and injuries. Additionally, documented rigging inspections are required for OSHA compliance and can help companies avoid costly fines.
In this episode of Safety Factor, we explore the critical aspects of rigging inspection safety, showing the crucial role of qualified inspections and third-party evaluations in ensuring compliance and preventing equipment failures. Rigging inspection managers Tom Horner and Bryan Holmgren provide an inside look at rigging inspections. With decades of experience between them, they reveal stories of dangerous rigging they have come across and stress the importance of Qualified, Competent inspectors to meet compliance and prevent catastrophic failures. Furthermore, they debunk the mistaken belief that all Competent and Qualified persons are equal, emphasizing the need for Competent, Qualified, and Certified inspectors with extensive experience to conduct thorough, documented rigging inspections.
When you look at the failure criteria for any type of item you’re looking at, alloy chain slings, it’s obviously written, and it’s objective. It tells you a gouge, it tells you a weld burn, it tells you heat damage. But when you start to look at them, it becomes subjective to the person, to the individual actually looking at it. What is a gouge to me, and what is a gouge to you? And how much of a gouge are you going to allow in service? And how much of a gouge am I going to allow?
Tom Horner, Corporate Rigging Inspection Manager-Rigging Inspection Services at Mazzella
Additionally, they address common excuses for using damaged equipment. Also, they explain the main qualifications and best practices for inspection companies to provide compliant, defendable documentation. With insightful tips on inspection program hurdles, building in-house expertise, and more, Horner and Holmgren make clear that rigging safety hinges on compliant and consistent inspection protocols.
What will you learn?
- Hear alarming stories of dangerous rigging found during inspections
- Learn what rigging inspection regulations and standards require
- Understand what to look for in an inspection company’s qualifications
- Discover common hurdles to starting an inspection program
- Get advice on how to build a compliant and defendable inspection process
If you are an EHS leader, safety manager, maintenance manager, or operations leader, this episode on rigging inspection safety delivers vital insights on establishing documented rigging inspection programs to ensure safety and regulatory compliance.
Transcript
Intro
And this is the truth. We were inspecting a beam, and the beam had very long chain attached to a master link and then the crane hook. Well, as the crane started to lift, the chain unloaded on the beam, off the beam, and the beam flipped over onto my foot. And through my steel-toed boot, it broke my foot.
Holy cow.
But I didn’t lose my foot because I had my steel-toed.
[Announcer] For your own safety, you are reminded to stand behind the yellow line.
[Ben Hengst] Welcome to Safety Factor, my name is Ben Hengst, and today we’re talking about rigging inspections. I’m joined by Tom Horner, Mazzella Corporate Rigging Inspection Manager, and Bryan Holmgren, Mazzella Regional Rigging Inspection Manager. Thanks for joining guys. Do you want to tell me a little bit about yourself? How you got started in the industry, a bit about your background, any funny stories you’ve had while you’ve been out on inspections or kind of is there anything that pulled you into the industry?
Who are the rigging inspection experts?
[Tom Horner] Yeah, I started with Mazzella back in May of ’95 and somewhere in ’97, ’98, I started to go out in the field to help with some inspections. And then it just kind of happened from there. There wasn’t really any decision or pathway, it was just, that was just what I ended up doing and I’ve been doing that ever since. I think the great thing about inspections is it’s not so much about the product we’re inspecting, but it’s about all the amazing customers we get to visit and what they produce and how they produce it. And we get to see their factories and the steel mills and the auto plants and the mom and pop shops. We get to see basically how everything is built or supplied to another vendor.
[Bryan Holmgren] So I came into Mazzella in 1998. I actually came into our chain shop as a welder in our chain shop, And I quickly moved into inspections by 2000. So basically, when you work in our chain shop, you quickly begin to understand inspections because there’s incoming repairs from customers. So I quickly learned how to inspect chains and slings and other rigging product as they were coming in for repair. And then opportunities opened up in inspections. We were growing in inspections. And naturally, like I said, I was already trained in that at that point and it seemed like a clear path.
How have rigging inspections evolved?
[Horner] Yeah, I think Bryan hit a really good point there. Back in ’97, ’98, ’99, safety was really just in its infancy, really across the country. Inspections weren’t rigging inspections, they were just alloy chain inspections. Customers didn’t have us look at their wire ropes and their synthetics and their shackles, and their below-the-hook devices. That all really started in the late ’90s, early 2000s, and that’s when we started to grow. We adapted, we prepared ourselves to be able to take on that type of inspection work. So like I said, way back in the day, we were only looking at alloy chain slings, and it was really based on OSHA 1910-184. Now you have the world of ASME. All of the standards are updated. A lot of different requirements. So a lot of evolution in in 25, 26 years.
[Hengst] What brought that change about? Did OSHA change the rules or did safety culture just change? Why did all of a sudden, there was a switch from just inspecting alloy chains to inspecting all of rigging?
[Horner] I think the safety culture at certain organizations was ahead of the curve. I can think of a few current customers in the Cleveland area that were way ahead of everyone else when they looked at their rigging. So, and I think the standards kind of caught up to them. OSHA really doesn’t write standards. They have some information, but they refer to the governing bodies and that’s when ASME was really coming into their own with the rigging standards, B30.9, B30.20, etc. And everything was just kind of written and caught up and revised. And we still see it today. There are still customers out there that are catching up to the standards.
How many inspections have the experts performed?
[Hengst] So how long have you guys been doing inspections? How many facilities do you think you’ve inspected in your life?
[Horner] Geez, I tried to run something. I’ve probably done 5,000 inspections. I can’t tell you how many customers. But I’ve been in nearly every major auto plant in North America. Stamping plants, the steel mills in some fashion, all the major manufacturing. ‘Cause we really built everything out of Ohio and expanded from there. So I can drive into nearly every city in Ohio and tell you where I’ve been. I could probably walk into facilities that I haven’t been in in 25 years and remember where all their rigging is at. And so it just… And you go to the customer’s repeat times. We have customers we’ve been doing inspections for for longer than I’ve been at Mazzella, so over 30 years. So we have a very long history. But, and how many pieces I’ve touched? Tens of thousands,
[Holmgren] Not quite sure on how many inspections. Definitely in the thousands. Pieces, I know Tom and I tried to figure that out in the past. Some guys look at 50,000 to a 100,000 pieces a year, some might be a quarter of a million pieces a year. So it could be in the millions of pieces we’ve looked at, easily. But yeah, I spent probably 12, 13 years in the field doing inspections. So in that time, easily, probably a few million pieces and a couple thousand inspections, easy.
What unsafe rigging horror stories have you seen?
[Hengst] So in that time, I’m sure you guys have seen some hairy pieces of equipment in the field, so you want to, without naming names of companies or anything like that, do you guys want to share some of the horror stories that you’ve seen in facilities, maybe in the early days or maybe even now?
[Horner] Oh boy, I got a couple that come to mind, is I remember a gentleman brought me a nylon sling that he had broken in half and bolted back together. And obviously, we see some incredible homemade devices, some of them engineered and looked very, very nice. And then you see some that were welded out of the back of a pickup truck in Upper West Virginia or something, you know what I mean? Just these horrendously fabricated devices. And then you see things, we’ve walked up, I think Bryan might have even been there with me. I’ve walked up to a chain sling and seen a link broken in half on an alloy chain sling as it’s hanging in use.
[Hengst] Wow.
[Horner] So you get out there and you just see all sorts of amazing stuff. Shackles welded together, homemade pins, just a little bit of everything.
[Holmgren] Yeah, I was actually going to use that example, Tom. I remember going out with a chain rep doing an inspection and walking up to a chain to inspect it after they just made about a 60,000 pound lift. And as I’m looking at the chain, as they’re starting to bring the chain down to inspect, there was a broken link in the chain. That was just one of multiple times I remember walking up and finding broken links in chain as they were in service and being used.
[Horner] I was doing an inspection at a customer, again in Canton, Ohio. And this is the truth. We were inspecting a beam, and the beam had a very long chain attached to a master link and then the crane hook. Well, as the crane started to lift, the chain unloaded on the beam, off the beam, and the beam flipped over onto my foot. And through my steel-toed boot, it broke my foot.
[Hengst] Holy cow.
[Horner] But I didn’t lose my foot because I had my steel-toed.
Hengst] Wow.
[Horner] We went through all the protocol and I had my foot in a boot because I had a fracture on the top of my foot that needed to heal. But all I could think about back then was, going back to the late ’90s, when I told you I had started doing inspections, I could walk into any customer, no safety glasses, no safety shoes, nothing but a Mazzella shirt and a clipboard, I could walk through the back door of any customer and just say, “Hey, where’s Joe Smith?” And people will just point you on your way and you just go meet him and do your thing. Now you come into 2024 and you get security badges, online training, drug testing, steel-toes, metatarsals, FR clothing, special gloves.
[Hengst] Hearing protection,
[Horner] Hearing protection. I mean, we are so far… We are so much more advanced than back in the day.
Why are these extreme violations being used in the field?
[Hengst] So when you come across these extreme examples, what are some of the excuses that you hear or reasons why these are still in use?
[Horner] Basically, it comes down just to a lack of training. How many times I’ve walked up to a user of a piece of rigging and they’ve asked me what we’re doing, and we’ll explain, Hey, we’re inspecting, we’re documenting, this is the requirements and your company’s staying in compliance, yada, yada. And they’ll say, “Well, how much is my chain… How much can I lift with my chain here?” And there’s a tag right here. They haven’t received even enough training to understand that the identification is required, but it’s also right in front of them. And then obviously, they don’t know how to do the calculations based on angles and whatnot. So really, it just comes down to when I get any kind of question, it’s almost always based around a lack of training.
[Hengst] And same for you, Bryan, is that the same thing that you’re hearing, they just don’t know, or is it?
[Holmgren] Yeah, or it could be that damage just happened, or are you sure that’s enough damage to pull that from service? What qualifies you to make that determination?
How to navigate objective standards in subjective inspections
[Horner] Yeah, this is a great question, and it’s actually kind of deeper. When you look at the failure criteria for any type of item you’re looking at, alloy chain slings, it’s obviously written and it’s objective. It tells you a gouge, it tells you a weld burn, it tells you heat damage. But when you start to look at them, it becomes subjective to the person, to the individual actually looking at it. What is a gouge to me and what is a gouge to you? And how much of a gouge are you going to allow in service? And how much of a gouge am I going to allow? And where is it on the link? Is it in the elbow, is it on the weld? Is it in a place that’s… The elbow’s the worst part. So and we get those questions and we do get challenges back, like what gives you the qualifications? So you explain our training and our experience and all that kind of stuff. But really it comes down to just laying everything out in front of the customer and just explaining to them, just look at what we’re talking about. Look at this interlink wear. When you move these links away, do you see how much is removed from this one? And also this link, and then this link and this. How much of that capacity have you lost just in total thickness of your item? And we can of course, get deep and deeper and deeper into all that conversation. But there is… It’s typically “oh that just happened,” or “somebody must have done that on third shift” or something.
[Hengst] So you mentioned that it’s objective, but then it can become subjective. So how do you think you look at things differently from the average worker subjectively when you’re looking at stuff? Are you more critical than they are or do you think that sometimes they’re more critical than you are?
[Horner] We get challenged both ways, actually. We’ll be challenged during an inspection that we’re being too critical. Or we’ll be challenged that we’re not being critical enough. Again, it’s what is a gouge? What is wear, what is that weld damage right there? Or a weld burn, or a cut in a nylon? What is that type of thing? So it comes back to, number one, there’s different environments, and we’re not strict or less strict in any type of environment, but we understand there are just environments that are very tough steel mills. And then there’s other environments that are generally more gentle on the items, but it always comes back to trying to work with whomever you’re having that conversation with, to train them, to educate them, “Hey, we’re looking at this one chain sling, if you want to give us a few minutes, we’ll walk you through how to look at this every day before you use it.” And give them that sort of off the cuff training, but information that they need to have in order to be able to use those items.
Just because it works doesn’t mean it should stay in service
[Hengst] And Bryan, when you get the excuse that it still works, what do you usually do to help kind of guide people into the understanding that just because it’s working doesn’t mean that it’s legal?
[Holmgren] Yeah, you kind of hit it on the head. If it meets the removal from service criteria, then that is what it is. We’re going to document it as such. We’re going to report it to our safety contact as such. So if you choose to keep using that, you’re going to be going against OSHA and ASME at that point and against your own safety department. So that’s a choice you’re going to make.
Will my rigging inspection be shared with OSHA?
[Horner] And that’s a really important piece is, when we’re doing an inspection for a customer and we’re looking at all their rigging, we’re telling them what passes or fails. We’re not an authority to tell them what they can use and what they can’t use. It’s still their property. Sometimes they do have to make that tough business decision, how do I keep myself moving forward knowing that you just… Not you, but knowing that we’ve damaged our singular piece of lifting equipment. How do I keep my operation moving? So we get a lot of pushback on that. Well, are you telling me I can’t do this? No, we’re just merely informing you. That’s what we’re here to do. The report we give at the end of the inspection is just a piece of compliance. What we’re… That’s actually the good stuff that’s happening is when we’re getting these questions, we’re revealing through this inspection where you’re really lacking: training, usage, care, that type of stuff.
[Hengst] Yeah, so Bryan, when you said we’re going to report to the safety person, you don’t mean OSHA, right? ‘Cause you’re not reporting to OSHA as rigging inspectors. You’re talking about someone within their organization, probably someone who’s brought you in to do the inspections, right?
[Holmgren] Yeah, it’s usually we’re dealing with a EHS leader, health and safety leader. And everything that we find on the inspection, we do report back to that person. So we would definitely report the deficiencies or anything that has been removed from service.
[Hengst] No one’s reporting to OSHA, no one’s-
[Horner] No, no.
[Hengst] You’re not going to tell on tell on anybody. You’re saying, “This has passed, this has failed.” Now it’s up to you as an organization to decide what you’re going to do with it.
How can rigging inspection reveal training gaps?
[Horner] Absolutely, like I just mentioned, when we’re there, we’re satisfying a compliance requirement. We got to put this piece of paper in your lap so you could put it in your file. But you still need to use that piece of paper to dig into what is your situation in your facility really like? Why is my failure rate so high? Why is it so low? Is my training grade… So many different variables. But that’s why you got to start digging in. So when we do get those interactions, we want to talk to them, “Hey, you have this failure. Here’s how we can address it. You need to do spares. Do you need a salesman to come in and look at application? Is it training on the care use and inspection? Are your people doing their pre-use inspections?” We want to get those conversations going from all of it. But no, we never reveal anything to anyone else for somebody’s inspection.
Why do businesses begin rigging inspection programs?
And even talking about OSHA, OSHA’s kind of dropped as this… Like we’re supposed to be afraid of them, right? And it’s really just not the case. We’re only talking about compliance. So in the sense of OSHA, I can’t tell you the last time that I’ve had a customer reach out to, at least me, and say, “OSHA was just in here, I got drilled. Can you come do an inspection?” Most of the time what we find from a customer is, “Hey, we were just bought,” or “we’ve got a new person who came into EHS and we’ve revealed that we’re lacking in our inspections and we need to get a program going. Can you help us do that?” Most of the big pushers of… Internal auditors are the toughest ones. They’re the ones within their own company that are going down to the maintenance staff or the EHS staff and drilling into the reports and the training and whatnot. So again, that’s why we love to have those conversations, ’cause we want to push them in that right direction. So if there ever was a case that OSHA had to talk to them about anything, all their ducks are in a row.
Are rigging inspections required by OSHA?
[Hengst] So when you say fulfilling a compliance requirement, are rigging inspections required?
[Horner] Yes. They’re required once per year, periodically, not to exceed 12 months. And that is a minimum.
What are the consequences of dropping a load?
[Hengst] So can you walk us through some of the consequences of dropping a load, besides the obvious of accident or injury? What happens if they drop a load and how can we help with that?
[Horner] Whenever there’s an accident, there’s a… Well within Mazzella, there’s a very specific protocol of how our sales supports that customer. But generally, the immediate effect is all workage has stopped. Everything is just, “we’re stopped. We’re not working right now.” So did they damage their crane? Did they blow apart a chain sling? Did they damage whatever they were lifting? Did they… Whatever kind of… Did somebody get hurt? That type of stuff. And then the questions start coming, “well, we need everything inspected. Where’s our reports?” Everything is just this tsunami of, “oh my god, we want our cranes inspected, our slings inspected. Where’s our training at?” You kind of just see this influx of people kind of running around with their heads caught off, trying to dot the I’s and cross the T’s when that should have all already been in place. But there’s also some other things is, when you hear about a dropped load, the first thing that I think about was what were they lifting with? ‘Cause if it’s a chain sling, those things explode and pieces go flying everywhere. So where did that link take off to that blew? Where did that hook take off to that blew? Did anybody get hurt? If it was a blown chain sling and the block flew up into the crane, what kind of damage did they do there? Who was close to it? And I think most of the time when you come to any kind of failure, the first response by the customer is, “it wasn’t our fault. The rigging was what failed,” or “the crane was what failed.” And the blame starts to go sort of into that direction instead of “what did we do wrong?”
What usually causes a rigging failure?
[Hengst] So if the rigging failed, though, usually… It’s not usually that the rigging’s defective, I would assume.
[Horner] Correct.
[Hengst] Usually there’s something that has gone wrong within the lifting process or-
[Horner] Yes.
[Hengst] Yeah.
[Horner] For all the years that I’ve been here and how many accident inquiries I’ve maybe been mildly a part of, I’ve never seen a defective chain sling, a defective weld, a defective link. I’ve never seen a defective nylon sling or defective sewing or a defective Twin-Path or shackle. It’s always come back to the process itself of moving the load.
Who can perform rigging inspections?
[Hengst] Bryan, who can perform inspections? Can anybody perform a rigging inspection or do you need to hire a specific company to do so?
[Holmgren] So there’s a minimum here, and then there’s what is the safe standard? What is the best practice? You need to be Competent and Qualified, per OSHA and ASME. Basically, you need the training. We take it a step further. We certify all of our inspectors. They go through thousands of hours of training. We take the stance on basically, you want to put your company in the best defendable position to make sure that the person doing that inspection knows what they’re doing, does it every day, and is going to come in there and make sure you’re compliant. We’re going to give you a compliant report, but you have to be trained, like I said, at minimum, Competent and Qualified. We just take it a step further.
Can documented rigging inspection be performed in-house?
[Hengst] Could you perform documented in-house inspections yourself?
[Holmgren] You can, as long as you’re Competent and Qualified and your employer is the one that’s going to name you Competent and Qualified and they have trained you to do such, you certainly could.
How do third-party inspections compare to in-house inspections?
[Hengst] So what are some of the differences that you see from in-house inspections versus third party inspections versus inspections done by someone like a crane inspection company who doesn’t necessarily specialize in rigging inspections?
[Horner] Oh, a couple of things. It’s very rare that you see any kind of customer doing their own inspections anymore. They’re still out there. Usually they’re much larger organizations. But it’s very rare. The problem you have with that is when you’ve taken a person or a couple people to do that for you, you’ve spent the money to train them and to travel them for the training and now you’re going to take them away from their full duty job to do this. You’re going to have to create your own documentation, complete that documentation and keep your own filing. So what happens when that person moves on, retires, transfers into another role? Internally, you’re going to have to go through that all again. So when you look at the cost of that to the cost of hiring a third party, that’s, I think, one of the main reasons why everyone goes third party, ’cause when they realize what they got to go through to do it themselves. Bryan’s exactly correct, Competent and Qualified OSHA, ASME. What we see, what I see is really too many people think that they can just do these because they haven’t studied the standards enough to understand what being Qualified and Competent is. And I’m going to give you an example. If you, Ben, went through training today and you went through three days of training and you put your hands on a bunch of different stuff and then one month later you actually did the inspection at your facility, you’ve done one inspection of X amount of pieces. Twelve months later you come back after not having touched one piece of equipment, how experienced are you? Was there new rigging introduced to your facility that you weren’t trained on?
[Hengst] So maybe on paper, I’m Competent and Qualified, but there’s a difference in standards between Competent and Qualified.
[Horner] This is why we love the term best defendable position, ’cause the way we’ve built our program is, as Bryan mentioned, when somebody comes into our group, we put them through a specific number of hours of hands-on with all the different products that they can touch. So that way when they’re in the customer for the first time by themselves, they’ve had a lot of experience with alloy chain and below the hook and lever tools and chain falls and shackles. They’ve… We can prove this, right? We can prove that this is all they’re doing every day. Not something that they’re called to do once a month, once every six months or once a year.
The importance of looking for specialized rigging inspections
And again, if you were only doing an inspection, let’s say you’re with a company that services cranes and you’re a top tech and you’re working on cranes all day, but twice a year, they ask you to come off the crane and look at rigging at two different customers. Well, if the rigging is not the same, how much experience do you really have of what you’re looking at? And then do you even know what you’re supposed to document and how you’re supposed to document? ‘Cause across all the standards, there’s different requirements. So again, our best defendable position is this is what we do all day, every day. We can prove this via paper trails, and everything we do is above or beyond what the standards require. So again, going back to the customer doing it themselves or any other entity, even if it’s a rigging shop, again, what makes… What is the proof of their qualification and competency?
How are Mazzella Rigging Inspectors trained?
[Hengst] So Bryan, you mentioned that at Mazzella, our inspectors get certified. What is the training process like for Mazzella rigging inspectors?
[Holmgren] So the very first process is we send all of our guys through a ITI-accredited institution to get training on anything below the hook. That’s a rigorous three-day course, hands-on, textbook, OSHA and ASME standards, learning all the nuts and bolts just to start. Then they really dive in and they get into the field and that’s when they get their hundreds and thousands of hours of hands-on under another Qualified and Certified inspector. That’s really when the training really takes off, so.
[Hengst] So it’s even once they go through the initial training part of it, then they actually go into the field with somebody else and they’re learning like a-
[Holmgren] Under another Competent, Qualified and Certified inspector.
[Horner] And there’s even another level that Bryan’s added to this is because our inspectors are staffed around the country, the types of customers that they see across the country are not the same in each region. There’s a lot more steel mills in Ohio and Michigan and Pennsylvania. Whereas in Florida, there’s not really any steel mill, at least how they compare to ours. So when we’re getting our techs through this process, we’ll actually make a concerted effort to look at where they’ve been in terms of what types of customers and we need to bring them into another state to work with another inspector just so they can see the different types of stuff in the different environments. ‘Cause again, they’re different across the regions. So we just want to make sure our… Our end goal is any inspector could go anywhere in the country and do an inspection, regardless of what they’re… Of who they’re visiting.
Is your rigging inspection report actually compliant?
[Hengst] And then I think that’s something that people don’t often think about. They know that they need a documented inspection, but the documentation isn’t necessarily always the same. Tom, can you tell us a little bit about some of the differences in inspection reports that you’ve seen in the past?
[Horner] Yeah. Oh God, give you our history. We were doing Excel spreadsheets back in the ’90s, and again, it was only alloy chain slings. And if you understand alloy chain slings, it’s got a unique serial number so it gets its own line in a report. Even if it’s missing its serial number and its tag, it’s still an individual item. And that’s what’s required for alloy chain slings. When you look at shackles, shackles don’t have a serial number, but they still require an inspection, but they don’t require documentation. But what’s the point of looking at it if you’re not even going to at least make a record? So to give you an example, if we looked at 24 one-and-a-half ton shackles, we’ll make that as a line item. 24 pieces passed or 12 pieces passed, 12 pieces failed. Just so that we have something. That’s where we’ve evolved over the years, ’cause we’re trying to stay ahead of the curve. If you’ve ever tried to get a report past an auditor, okay, you know you have to go above and beyond. ‘Cause no auditor’s ever going to say, “Well you said you looked at my shackles, but you don’t have it on the report,” right? So we’re trying to go be a little bit above and beyond. What I’ve seen in terms of, when when a customer comes to us for an opportunity and we ask them for a copy of a previous report, how many times I’ve seen a report, based on my experience, that would not be compliant to the standards is sort of mind boggling. Especially when you see that they come from some of the biggest names of any service providers in the country. Keeping it as vague as I can. I’ve seen reports that have said, “Listen, they said they looked at all your rigging and they gave you one paragraph that said they looked at 30 pieces of stuff.” Well, what is that stuff? Were there alloy chain slings in there? Were there twin paths? Were there lever tools and chain falls? Did they look at your shackles? Did they look at your eye bolts? This type of stuff. So, then I challenge back is, “Well you… I’ll give you this information, here’s the standards you can refer to. I would go back to that provider and say, ‘Hey, what did you actually do for me? ‘Cause you can’t prove anything by this report.'” And that’s the worst case scenario. I’ve seen some fine reports from the competition and a lot of people get it, but I saw a couple this year that, we won the opportunity for their business ’cause we were able to inform them about what they really needed to do and why what they weren’t receiving was compliant.
[Hengst] Without naming names, could you give some examples of that? What have you seen?
[Horner] Oh, geez, yeah. Again, very large crane service company was doing a rigging inspection, and a personal fall protection inspection too. I know we’re talking about rigging today. So when I looked at the report, the amount of information that was missing from the report, again, there was no proof of compliance. There was no proof that they actually looked at anything. ’cause they didn’t deal every detail, everything line item by line item. It was literally a paragraph at the end of the crane inspection report that says, “We did this, this, and this.”
How to be sure your rigging inspection reports will be compliant?
[Hengst] So what should customers be looking for when they’re looking for an inspection company? Specifically on documentation. Should they be asking to see a previous inspection report or an example of an inspection report? How can they make sure that the inspection report that they’re going to get is going to be compliant?
[Horner] Oh, absolutely. And again, our… The way we do things is we’re a little bit above and beyond with the way we try to document everything we touch, in some fashion. And really that’s all you have to prove back to the customer. Say, “Hey, if you look at this line item, this represents a chain sling.” And you’ll be able to explain that to them. To say, “Listen, across what we’re going to inspect is all your types of slings, your hooks, your below-the-hook devices.” Well, what is a below-the-hook device? We’ll explain what that really covers. “Lever tools and chain falls are not installed at height.” We’ll explain that. And then your rigging hardware. And then when we explain all that and you put the report in front of them and say, “This is technically what your report’ll look like if you have this stuff in your facility,” and that’s what’s going to prove the compliance. And then from there, you have the conversation of, “Well, what information does that report have that I need to bring to my leadership in terms of improvements? Is it more inspections, is it more training? Is it sales support on application?” All sorts of different questions.
What are the biggest hurdles to becoming OSHA compliant?
[Hengst] Bryan, what would you say some of the biggest hurdles are that companies face when they’re trying to become compliant, and how can they get over those hurdles?
[Holmgren] Taking that first step is the big thing. Starting the process is probably the tricky thing. Making sure you have spares in place, understanding that there may be a little bit of pain if there is that first inspection. There’s probably going to be things that are going to meet the removal from service criteria. We’re going to want to… We support you in every which way after that. We’re going to help you out with replacements, repairs, things like that. But the first inspection, once you get that under your belt, everything’s usually very smooth after that.
[Horner] Yeah, Bryan hit the nail on the head, is a lot of customers, it’s that first, let’s just get this one thing done first. Oftentimes, they’ll approach us with they want to be at the end before they’ve even started. You know what I mean? They kind of want to be done with this before they’ve even let us in the door to look at their stuff. So when we’re working with a customer in the beginning, it’s, “Hey, you need to give us an outline of what you have, a front load sheet. Just give us an estimate of what you have across the board.” And once they do that, and once we get in the door and we do that first inspection, it’s usually pain free from there, in the sense of you’ve already done all the hard work. Now you just have to maintain this year over year or month over month or whatever you’re doing.
The dangers of free rigging inspections
Also, there’s something I think it’s important to bring up in this conversation is, across the country for many years and even up until today, a rigging inspection was offered as a free service to many customers from, let’s say, a rigging provider, a rigging company provider. It was their way to maintain a relationship. It was their way to get in the door. But it was also a way to get more business. Because if I’m going to come in and I’m going to spend my day looking at your stuff and documenting it, all the repairs and replacements, it should come to me. We call that a conflict of interest agreement that we don’t entertain. All we care about when we’re there is to do a proper inspection and to get you compliant and to support you on the back end. If you want to spend money with us afterwards, fantastic. If you don’t, no problem. We’re here to help you be compliant, month after month or year after year. And that’s what we still see, again, across the country as a challenge is, “well, we always received them for free.” Well, how can you value the inspection if you’re unwilling to understand the investment we’ve had to make in order to create a defendable position for us to even do it for you?
[Hengst] And if it’s a free inspection, is it likely that the salesperson is also the person doing the inspection? Or do they usually also have an inspector come in and-
[Horner] Typically it’s a salesperson. Typically it’s a sales… Well, the way it was in the many years ago, it would be a salesperson and a representative from, let’s say, CM or a representative from Crosby, or back in the day it was ACCO or Peerless or whatnot, right? So they’d go in there and, again, they were only looking at chain slings. But then as this has evolved through slings all the different types of hardware, the support from the big companies like that has fallen to the wayside ’cause they’re not going to spend their time looking at anything else other than what they’re producing. So then it’s kind of evolved into a sales person and then they’ll just take some bodies from the shop. Hey, I need to take… Need to get this done for this customer. We’re going to be gone a half a day, a full day, or we’re going to… It’s a week long something or other. And again, what are they looking at while they’re there? And to give you one horrific story is, a customer called me out of North Carolina one time and said, “Yeah, our rigging provider came in and did my inspection and I found out halfway through my inspection that they weren’t looking at anything that wasn’t produced or sold by them.” So basically they were just walking through their shop and only looking at what had their name on it, in terms of rigging and everything else was just being left. That’s just a unique horror story. When it gets to any other service provider, I don’t care if it’s a tow motor company or a crane service provider or some other third party, if you take a guy off the crane and put him on the floor, is he really… Are you utilizing him to the best? And where’s that cost being hidden?
[Hengst] Yeah.
[Horner] Those are just honest questions you have to ask. And then again, what’s the proof? And I’m not saying anything against crane inspectors, they’re highly qualified individuals. I mean, they’re tradesmen of electricians and welders and mechanics and high level stuff. So it’s not that I don’t think that they can do it, but what’s the position that they can defend that allows them to do it?
Advice for starting an inspection program
[Hengst] Any advice for people who want to start an inspection program?
[Horner] Just like Bryan said, just do it. Get somebody in the door.
[Holmgren] Yeah, just reach out and make contact. And once you make contact, it’s pretty easy from there. We ask all the proper questions. We send you all the documentation, the front load sheets, We give copies of, or examples of our reports, training records. I mean, that’s ultimately the stuff that you’re looking for. And then to kind of piggyback off what Tom was saying, with crane inspectors going and doing inspections, 99% of crane companies don’t manufacture or sell rigging products. It’s usually just either they’re a crane service provider or maybe they do manufacture cranes. But 99% don’t even sell rigging. So there’s a pretty good chance that they cannot even supply you rigging on the backend or repair any of the product that they’ve pulled out of service. They’re probably going to send that off to a third-party provider because they can’t even handle that stuff for you.
[Horner] And then think about the cost of that. I’m taking something from you, I’m going to send it here, they’re going to give me a price, I’m going to mark it up, I’m going to send it back to you.
[Hengst] And the wait.
[Horner] And the wait. So there’s… Again, hopefully what we walk away from in this conversation is we’re just trying to inform people. There’s a ton of rigging inspection out there. We want as much as we can get. But we know other people… And on the customer end of things, we want them to be as informed as possible so that when they’re coming to us, they’re basically, “We know you, we’re ready.” And the inspection is really the easiest part of everything. It’s the Q and A on the front end that’s a little cumbersome at times. But once you get in the door… And we always encourage our customers, if we’re doing a first-time inspection or even if we’re there for the fifth year in a row, if you’ve got somebody you want to shadow us during an inspection, just so they can see what we’re looking at and how we move through things and why we do what we do, no problem. It is informal training, but it’s great to see from somebody else’s eyes, like Bryan had mentioned very early on, how many times I’ve been able to walk into a facility and I’ll see a chain on a crane 20 feet away, and I can tell that it’s stretched, I’m 20 feet away. You just get used to this. And it’s kind of the same thing. That’s how we need to get their operators in tune with what they’re doing. Every day when they come in, they know when their crane is acting up. They know when it’s drifting. They know when the brakes aren’t working. They know when it’s moving slow or it’s choppy ’cause they… Somebody jumped the rope on the drum, goofy stuff like that. We need to get them to understand that their rigging is just as important. And it just comes down to information. And anyone listening to this, I have to implore to you to research all of the content we have created for you. I don’t think there’s a question regarding rigging inspections or the rigging itself or how to inspect something or a standard that we haven’t answered somewhere, that you can use with your own people. It’s just there for you. And if you got any questions, I’m always receiving emails from you, Ben, “Hey Tom, can you answer this Q and A from YouTube or web question or whatnot.” We love those questions. Give us tough ones, too. Rigging inspections aren’t glamorous, they’re not fun. They’re usually painful, in the terms of customer has to spend some money at the end of it. But again, let us do the hard work for you and get you into a position where it just becomes something you do month after month or year after year. And let us, again, do the hard work for you.
How can you learn more about rigging inspections?
[Hengst] All right, thanks guys. So reach out to Tom or Bryan and as always, you can get ahold of any of our other experts at MazzellaCompanies.com. Don’t forget to pop into our learning center. Tom’s right, we have a ton of information on rigging inspections there, including free eBooks, courses, articles, and videos. Subscribe to Safety Factor wherever you listen to your podcast, or you can watch it on the Lifting & Rigging Channel on YouTube. Thanks for listening, stay safe out there.
Guests:
- Tom Horner, Corporate Rigging Inspection Manager-Rigging Inspection Services at Mazzella
- Bryan Holmgren, Regional Rigging Inspection Manager-Rigging Inspection Services at Mazzella
Background Reading:
- OSHA Inspection Series: How Important Are Rigging Inspections?
- At least one periodic inspection of your rigging equipment is required every 12 months (at a minimum) per OSHA and ASME. Learn more about inspection frequencies and the factors that can affect the cost of a periodic rigging inspection. How Much Does an OSHA/ASME Compliant Rigging Inspection Cost?
- These four simple questions can help make your rigging inspection run as smooth as possible and avoid surprises and extra charges during the course of a third-party rigging inspection. How to Plan and Prepare for a Third-Party Rigging Gear Inspection
- How do I know if I received a good rigging inspection that keeps me in compliance with ASME standards? What Signs Will Show if My Rigging Inspection was ASME-Compliant?
- What to look for when selecting a third-party company to inspect your wire rope, chain slings, roundslings, and rigging hardware. How to Choose a Rigging Inspection Company for OSHA Compliance
- Sling Inspections, an online Lifting U™ course, is designed for anyone looking to learn how to inspect their lifting slings to OSHA & ASME standards. Mazzella Companies Launches Online Sling Inspection Course
- Depending on the severity of the operating environment and frequency of use, your business may choose to integrate a more thorough and more frequent rigging inspection program. How Often Must Slings and Other Rigging Equipment Be Inspected?
- Identifying and removing unsafe lifting and rigging equipment is critical to a safe work environment and avoiding accidents and costly fines. Do You Know What Damaged and Unsafe Rigging Equipment Looks Like?
- No matter what the production process is, what’s being moved through the facility, or what type of rigging practices are being used, these are the most common problems we discover during the course of a rigging inspection. The 6 Most Common Problems Found During a Rigging Gear Inspection
FREE Downloads:
- Sling Inspections E-Book: A Guide to Inspections & Applicable Standards
- Rigging Gear Inspection Field Reference
- Lifting & Rigging Inspection Frequencies & Records Guide
- Harness Inspection Checklist
- Mazzella Cable SRL Field Inspection Reference Guide
- Synthetic SRL / Lanyard Inspection Checklist
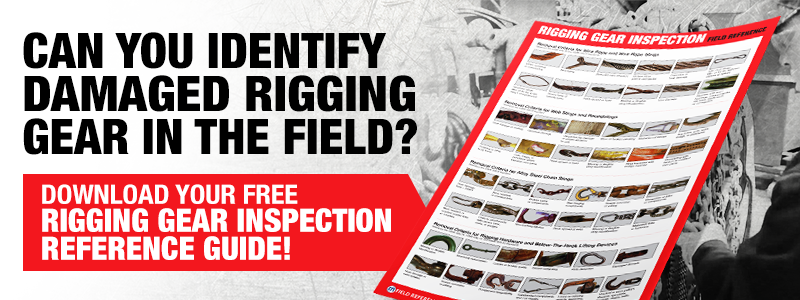
Related Podcasts:
Contact Mazzella:
Schedule Remote or In-Person Rigging Training
Contact Mazzella’s Overhead Crane Division
Subscribe wherever you listen!
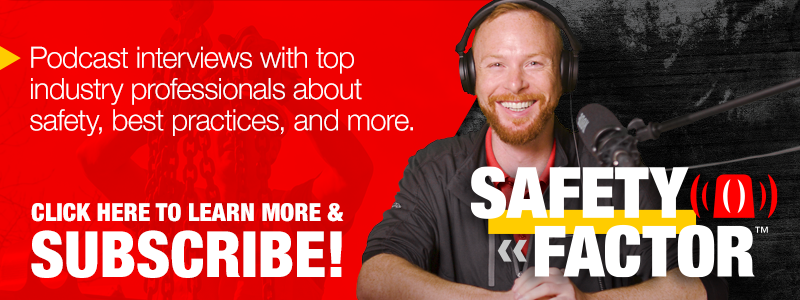
In This Podcast:
0:00 – Intro
0:59 – Who are the rigging inspection experts?
2:47 – How have rigging inspections evolved?
4:34 – How many rigging inspections have the experts performed?
6:06 – What unsafe rigging horror stories have you seen?
9:11 – Why are these extreme violations being used in the field?
10:31 – How to navigate objective standards in subjective rigging inspections
13:19 – Just because it works doesn’t mean it should stay in service
14:01 – Will my rigging inspection be shared with OSHA?
15:41 – How can rigging inspections reveal training gaps?
16:29 – Why do businesses begin rigging inspection programs?
17:39 – Are rigging inspections required by OSHA?
17:52 – What are the consequences of dropping a load?
19:26 – What usually causes a rigging failure?
20:29 – Who can perform rigging inspections?
21:30 – Can documented rigging inspections be performed in-house?
21:47 – How do third-party inspections compare to in-house inspections?
24:39 – The importance of looking for specialized rigging inspections
25:34 – How are Mazzella Rigging Inspectors trained?
27:34 – Is your rigging inspection report actually compliant?
31:04 – How to be sure your rigging inspection reports will be compliant?
32:24 – What are the biggest hurdles to becoming OSHA compliant?
33:58 – The dangers of free rigging inspections
37:38 – Advice for starting a rigging inspection program
41:34 – How can you learn more about rigging inspections?
Disclaimer:
Any advice, graphics, images, and/or information contained herein are presented for general educational and information purposes and to increase overall safety awareness. It is not intended to be legal, medical, or other expert advice or services, and should not be used in place of consultation with appropriate industry professionals. The information herein should not be considered exhaustive and the user should seek the advice of appropriate professionals.