Safety Factor: Steel’s Sprint From the Safety Stone Age
Steel mill safety has come a long way! The “hot, nasty, dirty, and dangerous” mills of yesteryear were all about tonnage. But now it’s people over production.
In this episode of Safety Factor, we follow steel mill safety’s fiery trail from OSHA to smart sensors. Three mill veterans bare their battle scars from the early days. We’re talking about tearing your rotator cuff atop 3,000° furnaces. No tie-offs, no fall protection, no nothin’. Just sweat and steel. How has steel mill safety evolved and improved over the years?
Today it’s a new safety culture focused on planning, training, and prevention. VR simulators, automated cranes, and “no-touch” tools help avoid hand crushing and drops. Real-time data guides continuous improvement. And cardinal rules weed out the reckless.
Steel may still run thick in the blood, but now there’s pride in steel mill safety records too. Far from the Wild West, modern mills blend tradition with technology. Protecting their tribe, sharpening their edge. How are steel mills becoming safer and more modern workplaces?
Join Michael, Jim, and Chris as they temper their decades of expertise. We examine past pitfalls, current challenges, and the high-tech future. How to keep good people safe – and build quality faster than ever.
So heat things up with us! Learn why steel mills are becoming safer, smarter workplaces while staying productive. Learn how the steel industry is evolving to protect its people and retain its proud traditions. In this episode of Safety Factor, experts examine progress in safety procedures, training, equipment, and culture. It’s all here in this edition of Safety Factor!
Transcript
Safety Factor: Steel’s Sprint From the Safety Stone Age
– [Jim Warren] In the steel industry, you’re not making pillows, right? So, you’re, it’s hard work. The, the environment is hot, nasty, dirty, and inherently dangerous, right? So, I mean, you’re dealing with, in the melt shop, you’re dealing with steel up to 3000 degrees, you know, everything’s heavy. For your own safety you are reminded to stand behind the yellow line.
– [Ben Hengst] Welcome to Safety Factor, my Ben Hengst, and today we’re talking about how we can create safer steel mills. I’m joined by Michael Skipper, general supervisor of Rail Mill Operations at EVRAZ North America, a leading producer of engineered steel products for rail energy and industrial end markets. Mazzella’s Jim Warren, Director of Steel Segment, and Chris Ross, Mazzella Key Account Manager for steel sales. Thanks for joining, guys.
– Thanks.
– Very welcome.
– Glad to be here.
– [Hengst] Can you guys tell me a bit about your background working in the steel industry? Mike, we could start with you.
– [Michael Skipper] I’ve been in the steel business for 18 years. Started out as a crane technician, so I’ve worked with numerous service companies and eventually moved into some maintenance and reliability positions internally within some steel businesses, as in such EVRAZ steel here in Pueblo, Colorado.
– [Warren] Myself, I’ve been with Mazzella for a year. Before that, I was at a crane service company for 19 years. Serviced steel mills, aluminum mills, paper mills. And then prior to that I worked for a steel mill for nine years. Spent four and a half years in the rolling mill, and four and a half years in the crane department.
– [Chris Ross] Myself, 12 years I was in the graphite electrode business, production and sales of, of graphite electrodes. And then prior to that, since 1993, I was in with a leading steel pro, with a steel producer in the melting, melting area. Started out entry level in the melt shop, and then left as a melting supervisor in 2011.
– [Hengst] Okay, so what are some of the most significant safety concerns associated with steel mills today?
– [Warren] Well, the, the biggest thing that everybody’s pushing right now is no touch, right? So people, they’re trying to get, trying to get the people away from the, the, the safety concerns and the safety hazards, right? So whether it’s no touch tools for lifting and rigging, no touch electrode handling, that kind of thing. That’s, that’s, that’s the biggest thing that I notice right now.
– [Ross] No, I agree, I agree. I think, you know, also one of the concerns is, is they’re, they’re, it’s, it’s the elimination of hazards. So if they can’t eliminate ’em, then they’re trying to mitigate ’em the best they can. That Jim mentioned with tools, process, procedures that they can use.
– [Hengst] So what are some of those hazards that we’re trying to eliminate or mitigate?
– [Skipper] I think it’s, it’s overhead cranes, right? I think it’s lifting equipment. I think there’s slips, trips and falls.
– [Warren] Hand injuries.
– [Skipper] Walking working surfaces, hand injuries.
– [Warren] Yeah.
– [Skipper] Things like that, right? I mean, it’s, we’ve used quite a bit of the no-touch tools, you know, within our facility, and I think that’s helped us reduce some of our safety incidents surrounding hands drastically, you know, by keeping the team members’ hands away from the hazards, right? You’re not picking up chains, you’re not moving the load. You actually have something to push and pull with versus having your hands do that work for you.
– [Warren] Yep. One of the, one of the things, that has always been one of my favorite sayings is, you know, in the steel industry, you’re not making pillows, right? So you’re, you, you’re, it’s hard work, the the environment is hot, nasty, dirty, and inherently dangerous, right? So, I mean, you’re dealing with, in the melt shop you’re dealing with steel up to 3000 degrees, you know, everything’s heavy. There’s, there’s nothing that’s not heavy, right?
– [Ross] Yeah, everything’s heavy. You’re dealing with high power, high temps. So you’re, you’re like, Jim says you’re, you’re in a, a, a zone that’s inherently dangerous when you’re just trying to-
– [Skipper] And when you go to use it, you want it to be safe the, the first time, right?
– [Ross] Right.
– [Skipper] You don’t have that second chance or second opportunity to make sure that you do something correct, right? If you don’t do it right that first time, it could potentially, you know, cause a major risk or impact to you or the, the company or your team.
– [Hengst] Okay, so speaking of, you don’t want to do something a second time, let’s talk a little bit about the history of steel mills. You know, historically, I know that steel mills have not been the safest place, and you know, in 1970 when OSHA was established they became significantly safer. Can you walk us a bit through the history of steel mills and how they’ve improved today to become safer work workplaces?
– [Warren] Well, I can tell you the mill that I worked at, in 94, when I started, we really didn’t have safety, safety harnesses, right? Man lifts. You got in a man lift and you just went up. Right? If you needed something moved, you just, you just grabbed it and moved it. Right? There was no SOP or, or anything that was a safe procedure to be able to- JSAs even, right?
– [Skipper] Yeah.
– [Warren] How, how, how many, how many JSAs do you guys have today versus when you first started, right?
– [Skipper] Absolutely. That’s something we preach to our, our new hire team members, right? As soon as they come in the door, just they’re going through their, their new hire training right? Is looking for those hazards and what can we do to assess ’em and mitigate ’em.
– [Ross] Yeah, you’re right. And it’s like Jim’s point, I know that in the early 1990s when I started, it’s not that safety wasn’t important, but, at the time, the, the, the push was on for production. I mean, safety was mentioned, safety was discussioned, but, it was not the par- didn’t have the focus or the push that it, that it really does now. And that’s, that’s evolved over time. You look at the severity of the injuries dramatically reduced over time just because the refocusing and re-shifting to that “be safe”, you know?
– [Skipper] I think training’s came a long way too. You know, I think years ago it was not so much a forefront of our mind, right. Of making sure that, you know, we trained in forklifts, or we trained in cranes, or we trained in rigging, and, you know, you had this small group of training, but nothing as vast as it is now or in depth, for that matter.
– [Warren] Yeah.
– [Ross] Well, then, then requiring their certifications, the guys have to be signed off.
– [Warren] Yeah.
– [Ross] I mean, you know, if you’re not signed off, you don’t do it. If you’re not qualified, you don’t do it. You know, in the early days of steel mill, you, you were-
– [Skipper] Just did it.
– [Warren] Yeah you just did it.
– [Ross] You were just a jack of all trades.
– [Warren] Something was in the way you did it right? If there was, you know- Now don’t get me wrong, I’m not saying in the, in the mid nineties, it was as bad as before we even had OSHA when you had, you know, there was 30 guys waiting at the gate for a job, you know what I mean? And somebody died and they were like, “Oh, grab, grab Ben bring him in now.” Right? It wasn’t that bad, but, like I said, it was, it was just, you just did what you had to do in order to get the product out the door.
– [Ross] Yeah, the focus was on operations, tonnage. I mean, you were focused on tonnage, and you wanted to be as productive and efficient and, no time lost. I mean, and it’s, it’s really been amazing to see over the past, and really specifically, over the past five to 10 years, the absolute re-shift in the industry.
– [Warren] And don’t, and don’t get me wrong though. I mean, it’s, I I’m not saying that’s a bad thing.
– [Ross] No.
– [Warren] Right? But when I was talking about like, JSAs, right? I mean, you know, just, just over the years that I’ve spent and the amount of JSAs and the procedures pre-job, right? Pre-job procedures and everything that you go through, lift, lift plans.
– [Skipper] Yes.
– [Warren] All that stuff now, you know what I mean? All that is a good thing, right? Because not only does it help with safety, but it also helps with free planning the whole project itself and, and seeing what’s going to happen, how long it’s actually going to take, how much it’s actually going to cost.
– [Skipper] Yeah.
– [Warren] Right? To to, before it was, like I said, get it done. Oh, you need a crane, you need to put the crane up? You run outside, you grab the 65 ton RT, you bring it in the bay, and you pick up whatever it is, and you’re like, “Oh, crap, I forgot to put this, I forgot to put the outriggers out”, or, you know, it was, it was just whatever, right?
– [Skipper] And I think it came along too with the more we understood human behaviors, right, and, and understanding exactly, you know, how our brains function and what amount of risks, you know, that we induce ourselves.
– [Warren] Yeah.
– [Skipper] By not being repetitious in, in how we move or how we operate.
– [Warren] Yeah.
– [Ross] And, and it goes back to where when you, like Jim says, when you plan these jobs now, when you, when you follow the protocols, you can actually identify potential delays, potential hazards. So you can time your job much better than, than you did in the past. Where you would guesstimate an eight hour job, not foreseeing, you know, what could happen, and that eight hour job becomes 12 because you didn’t plan for certain things. It helps a lot with the planning, moving forward.
– [Warren] Yep.
– [Hengst] So what do you think helped refocus the industry? Like what changed that that mindset?
– [Ross] That’s a, that’s you, I don’t know, I don’t know if there’s one thing that you could look at. I believe corporations started paying a lot more attention to, you know, lost work time, like day’s injuries. I mean insurances. I mean-
– [Warren] I was getting ready to go there. It was insurance, right?
– [Ross] Insurance is a huge motivating factor.
– [Warren] Insurance, workers’ comp, all of those things right?
– [Ross] Exactly.
– [Skipper] I think we started to realistically view what that full cost of safety looks like.
– [Warren] Yeah. But, but when they started having to record, record all your numbers and all your data and everything like that, and it, again, I, I’m not saying that companies didn’t care about you, but when they started seeing all that data in front of ’em now, right.
– [Skipper] That transparency.
– [Warren] Yeah, right? And even in 94, when I first started, we had computers, of course, right? But we weren’t into ’em the way that we are now.
– [Ross] Right.
– [Warren] Right. Everything now is, is, is logged and, and entered into the system, whatever that is. And then once they see all those numbers and they see, oh, oh crap, we had, you know, across our organization, we had 200 hand injuries over this last year because we were pushing and pulling, crane moves and everything like that. That’s real data. That’s, that’s live data that’s actually happened to their people. And now when you bring that up to the, to the, to the upper echelon management, now they’re like, “Okay, we got to do something.”
– [Ross] Well, it’s, it’s like society too. I mean, society’s become so hooked on analytics. Analytics drives everything. They want to know anything that they can document, anything that they can put numbers to, they’re putting numbers to. And, and this was a huge push for them as well, to, to document and, and trend. Like Jim said, they trend it, and what can we do? It’s not, it’s not only as important to be the most productive facility in the world now, it’s, it’s also a, a, a, a medal or an honor to be the safest.
– [Skipper] The safest.
– [Warren] Yeah, for sure. Yeah, every mill that I, I mean, I can’t, last year, last year alone I think I went to 20, 26 different mills in the country. Right. And every single one of ’em, I don’t care where I was, the first thing you see when you pull under the gate, is lost time accidents.
– [Skipper] Yeah.
– [Warren] And then how many days it’s been since their recent. Most of them were zero. You know what I mean?
– [Ross] That’s good.
– [Warren] Zero as far as zero accidents. Right?
– [Ross] Right.
– [Warren] But it’s been, you know, you know, 300 days or 200 days or whatever. So, they’re, they’re, they’re proud of that number now because that means that, hey, not only do we do, we take care of and, and pay our people well, but also we’re, we wanted to make sure that they go home to their families at night. There’s a, there’s a, there’s a large steel company that, that starts with a letter “N”, and every one I go to, they have, on one of the buildings, now I’m talking the buildings outside, they have pictures of their employees and their kids. I mean, that, that, that says a lot.
– [Skipper] Well, I think that’s probably a fair thing, right? Is that the shift was probably largely due to the, the care for people. I think when the care for people changed versus the care for tonnage changed, I think that’s where we started getting some of those things where we took pictures, where we were proud of our families, and proud of our teammates, and proud of the numbers that we achieved on, on being safe and going home every day with all of our fingers and things like that. But also in doing that, you’re producing.
– [Ross] Yeah.
– [Skipper] Right? ‘Cause the safer you are is proven that the, the more effective you are at productivity.
– [Warren] Yeah.
– [Ross] I agree.
– [Hengst] So what are some of the technologies that are being implemented in steel mills now that’s helping make them safer, workplaces safer for the employees?
– [Skipper] I like some of the, the forklift hidden sensors and things like that. Where you come around some of the corners and as soon as it picks up on a, a body or, or some type of an object, the lights go off and it flashes and some kind of a, a sound, you know, goes off to let you know that, hey, someone’s around the corner, or forklift’s coming, or something like that. I think that’s huge. I can’t tell you how many times I’ve been inside of a shop and you’re going through a walkway, you open up a swing gate thinking everything’s okay, and as soon as you step out, all of a sudden, boom, here comes the forklift, or even a person. Right, then you walk into another individual.
– [Ross] Yeah.
– [Skipper] It happens more than, than we think about, right?
– [Ross] And you bring up a good point too, think about it, guys, it wasn’t that long ago, we didn’t even know what a swing gate was. We didn’t know what a dedicated walkway was.
– [Warren] Right, right.
– [Ross] Right. We, and it’s, it’s that shift. And then you’re also getting into so much, the industry’s progressing and the availability of products is progressing so fast, to go to automated systems and preventative systems. We, we’ve got a number of them ourselves that we, that we can provide for customers.
– [Warren] Some of the things I’ve done in the past, I’ve, I’ve put lasers on the crane, right? So they, they’re laser indicators on the floor, light sys, light systems, that run the whole bridge of the crane, right? So they light up, they illuminate the floor wherever the crane is. Audible alarms, you know, crane 21, moving west. It would actually enunciate that throughout the plant. Like I said, just different alarms, put in limit switches on different parts of the runway that actually lower gates. I mean, there’s a lot of automation and stuff like that that can go into this.
– [Skipper] I think some of the coolest things I’ve seen in the crane business is some of the electronic pre-shift inspections for the cranes, to where they’re, they’re tied into the crane itself so that you can’t actually operate it until you complete that inspection. So you ensure right, that the team members that are, you know, operating these pieces of equipment have went and visually verified that some of these things are safe, you know, not only for themselves, but the teammates around them that are working in that area. So I think that’s pretty cool.
– [Ross] Oh yeah. Like I said, the automation is limitless. I mean, the engineering, you young guys, are coming up with some really cool stuff now.
– [Warren] You whipper snappers.
– [Hengst] And Jim, you mentioned the no touch systems before. Can you tell me a little bit about like what, what exactly are those and how do they work?
– [Warren] Yeah, so with lifting and rigging, we’ll start there. So, you know, you have push pull tools, right? They’re basically big hooks and it can be various lengths. And that’s, so you can keep your hands, hands away from, you know, heavy objects, right? So if you’re, if you’re picking something up with an overhead crane, a forklift, anything, right? You would utilize these no-touch tools to reach out, grab that piece of equipment. So now it’s putting distance between, you know, soft flesh and a, and a, a, a steel object or whatever, right? Then we look into our electrode handling business and we have the, the no touch system with that. We, we completely take the, the, the floor, the the melt shop day guys and, and, and everybody out off the floor, and we’re doing everything on that with the crane, right? So we’re adding stick to the column to be able to continue melting steel. But we do all that through that no-touch system, right? We, we completely take everybody away from that. So there’s no human interaction that’s required.
– [Skipper] And I think that helps too, as, you know, more companies develop, you know, sway control systems and things like that for overhead cranes. You don’t have the risk anymore of, you know, operators or new operators, you know, as they, you know, progress into these cranes, they’re, they’re swinging the loads or they’re swinging the hooks into trying to-
– [Warren] You talking about, about smart features, kind of?
– [Skipper] Yeah.
– [Warren] Okay. Yeah, yeah.
– [Skipper] Yeah, as they’re controlling the trolley and bridge and things so there’s not so much of a swing of the, the load block, right? You’re able to smoothly control how you hoist into something and pick up something and control that load wherever you’re taking it.
– [Warren] Yeah, especially with the cranes, right? So that was another thing that we used to do, and we, we still do with Mazzella is, you know, we have no fly zones where we can actually take an object if you have a building or if you just wanted a temporary object, right? We can make the crane, you can run the crane as fast as you want, and it gets to a certain point, it’ll actually slow down and stop, until you go around it. Right? We can make that permanent or temporary. What, anti snag, right? So that’s a big thing in the automotive industry. You know, they, they leave the slings attached to the dyes, unfortunately sometimes, and then they’d go to bridge and they’ll actually flip it over. So, once you get to a certain degree of side pull, or side load, on the, on the crane, it shuts it off. So yeah, there’s all kinds of smart stuff out there for that.
– [Ross] I think, I think one of the coolest things too that we’ve come up with is that electrode adding process. I mean, being a, being a former steel producer, probably, you know, used to climb on top of the furnaces, you’re, you’re on top of a 3000 degree oven, basically, making steel.
– [Skipper] Pretty much.
– [Warren] You did your adds on top of the furnace?
– [Ross] Yeah.
– [Warren] Yeah?
– [Ross] When we first started. And you know, you’re walking that narrow arm, carrying a chain wrench, and you’re flying in a 3000 pound electrode hanging over your head, screwing it together with a chain wrench.
– [Warren] Hey Chris, what, what were you tied off to?
– [Ross] We couldn’t even spell tie. That’s the, you know, and, but it was the process, right?
– [Warren] Correct. That’s how you did it.
– [Ross] I mean, it’s, it’s, it, it wasn’t that we were circumventing anything, it was just that, that’s the way it was done. And that was, and it’s, you know, when I can remember going to the first, when we, the early automation or early robots, everybody complained about the additional time, right? First, oh, it’s taking me- we used to be able to run up there and add a stick in two and a half minutes and be down, power back on. Now it’s taken us four and a half. Well, it’s like anything else in the steel industry, right? You work with it enough, you get the times down.
– [Skipper] That’s right.
– [Ross] And not only that, I mean the, the potential for injuries, I mean, I think, I think I know twice I tore rotator cuffs and shoulders, jerking on wrenches and sand buckets before we had automation.
– [Skipper] Think about what that would’ve saved, right?
– [Ross] Yeah, exactly.
– [Skipper] What if it would’ve been the, the last tear?
– [Ross] Yeah.
– [Skipper] You wouldn’t have been able to use that arm again, right? And that’s the, that’s what I think the focus is, is we can’t forget about making sure that, you know, it’s, it’s people, and at the end of the day it’s people driven. So if you would’ve lost that arm, you know, what about grabbing your, your wife or your grandkids or something like that, right? You lose that ability. So making sure that we gain that opportunity back without having that risk out there is, is huge.
– [Ross] Yeah, and then you also look at the simple fact, it makes guys more aware of their job when they’re having to run that piece of or operate that piece of equipment. They’re not as complacent as they were in the past. I mean, unfortunately, one of the last electrode additions I made on top of the furnace, we were sent out there with the power still on. So, I mean, you’re talking about what, 34,500 volts, it’s live coming in and miraculously neither one of us were hurt, but you know, unfortunately, people get complacent in a routine or if they’re running that equipment, or if that equipment is basically running itself.
– [Skipper] Yeah.
– [Ross] Guiding itself. You take that potential hazard out, you eliminate that.
– [Warren] Yeah.
– [Ross] So.
– [Skipper] Well what you mentioned, is something that it has been more of a known now, within the crane and steel and, you know, business is, is tie off, and fall restraint and fall rescue systems and things like that, you know?
– [Warren] Yep.
– [Skipper] Years ago you said you wouldn’t really see a, a harness, right? Now you’re starting to see cranes and things like that becoming, you know, sold within packages of ensuring that we have, you know, horizontal lifelines and things like that with them. So as you know, that, you know, maintenance team members and operators and things like that, as they board ’em, they have that ability.
– [Warren] Like I said, when I started, I mean, it wasn’t, I mean, to get a, to get a harness was, they’re like, you know, “Why do you, why do you want one of those? You wuss.” You know what I mean?
– [Ross] Yeah.
– [Warren] But, but now, try and try and go four over four foot off the ground and, and have somebody see you,
– [Ross] Yeah, I dare you.
– [Warren] in a mill,
– [Ross] I dare you.
– [Warren] and see what happens, right? I mean, now four foot off the ground and they’re like, “What are you doing? Get out off my mill.” You know what I mean? You got to be tied off, what are you doing. So…
– [Ross] Yeah. And it’s, it’s so funny. I mean, things that we all kind of didn’t think about, you know, just simple stuff. The, the, the, the apparel that we wear, the, the, the PPE that we wear. I mean, we, we laugh ’cause back in the day we didn’t have those options. I mean, yeah, you had a hard hat and a jacket, but you didn’t wear FR clothing, you didn’t have any of that stuff. It was just, but that, that, that goes back to what we were talking about earlier. The, the focus shifting back to taking care of your people and that becomes the cost associated, it’s a whole lot easier to keep ’em safe and healthy than it is to pay for an accident.
– [Warren] Yeah.
– [Skipper] Well, we have cardinal rules now, right?
– [Warren] Yeah we do.
– [Skipper] That we train our team members on. So you don’t have that ability anymore. You know, if you do break that, that four foot rule, you’re gone. Right? There’s no question whatsoever. If you do certain things, if you cross overhead crane, you know, guardrail systems, right? That’s a cardinal rule. You, you’re no longer employed. You know, some of those things that are, you know, put in motion now that turns us away from taking that, that shortcut and trying to speed that time back up that, you know, we think in our mind we’re losing, but we’re not actually losing.
– [Ross] Right.
– [Warren] Well part of that has to do with, they want to make sure that the consequences are severe enough that, that you understand, they know they care about you. Does that make sense?
– [Skipper] Yes.
– [Warren] Right. I don’t don’t think that it’s, they don’t want you to not be safe, or they don’t want you to be safe because they’re worried about their numbers. I know we said that earlier, as far as kind of what brought that around nowadays. But the bottom line is, is, is they want to make it severe enough that you understand that, when you do that, it is, it, the end result or the consequences that can be involved in that are so much worse than, you know, anything else that…
– [Skipper] Yes.
– [Warren] If you screw around and you do this, that’s, that’s that cardinal rule, you’re going to, you’re going to get kicked out of here.
– [Hengst] Yeah. You need, you need to get out before something actually happens to you.
– [Skipper] Yes, right.
– [Hengst] Because obviously you don’t understand.
– [Warren] Exactly.
– [Hengst] Your own safety.
– [Ross] We’re not- And it’s, and it becomes, like you said, then it, it is, it’s, the focus is not, “Hey, you’re going to make us look bad.” It’s, “We’re we’re going to prevent you from tragically harming yourself or, or losing your life.”
– [Skipper] Or anyone else.
– [Ross] Yeah.
– [Warren] Yeah.
– [Ross] And it’s preventative.
– [Hengst] So what are some of the barriers that might be there for some steel mills starting to adopt new technology? I know that historically steel mills have been kind of slower adopters of technology. So, what are some of the barriers and what can, how can people help push past those?
– [Skipper] I would say from my experience, it, a lot of it surrounds cost, right? When you start getting into some of the older facilities, trying to upgrade them or modernize them to the, the ways that we are, are, are facing now is quite difficult. Because you’re talking about an exuberant amount of money that has to be, you know, projected out into, you know, a billion dollar facility. So how do you do that in waves, right? ‘Cause we can’t just come up with a billion dollars and say, here you go, you know, let’s just upgrade all these cranes, or upgrade this furnace, or upgrade these mule stands or what, right? But I think a lot of it surrounds what you mentioned earlier was, you know, procedures and policies and going back to the training, you know, ensuring that we put some formats in place to kind of mitigate some of those things.
– [Ross] Right.
– [Skipper] And train against them. Until we can slowly project that money where it needs to go.
– [Warren] So, so, tell, tell everybody real quick, what’s, what’s some of the things you implemented as far as training at EVRAZ?
– [Skipper] So, well, we went down the, the route of having a virtual reality crane simulator, which I think is a great resource and tool to have, and we started using it to gauge some of our operators as they were coming on board to become qualified crane operators, where, you know, the, the virtuality simulator simulator with ITI, has a scorecard, to me is similar to Amazon, right? You’ll get a one, two star, three star type deal as you go through each course. And I think it relates to the team members that we have, as a younger generation in the workforce, they understand electronics, they understand the games. So it’s relatable. But yeah, as you go through each course, you’re able to, to train on it, it gives you a score. Let’s say you’re at a one star, two star, three star, and as you pass on, right, you go to the, the harder or more strenuous type crane operations. And I think it’s proven tremendous results, for sure.
– [Warren] Now are you still doing, like, hands-on operator training too?
– [Skipper] Yes. So we do have like a daily course of cranes and rigging, that we developed with ITI as well, that goes through, you know, overhead crane, you know, inspections, what are some of the hazards, you know, what are some of the things to look for, and you know, how we could be better at operating these dangerous assets.
– [Warren] So are you, are you guys doing that with everyone, or just, just the crane operators?
– [Skipper] Well, I think back to what I said, you know, with a slow progression. So we tackled first, all of the new hire operators.
– [Warren] Okay.
– [Skipper] And then we went into the maintenance personnel. As we seen that was the risk, we, you know, we were not covering, making sure some of our maintenance personnel that, that dealt with these cranes-
– [Warren] ‘Cause they’re going to use the cranes during a downturn or what- Okay, okay.
– [Skipper] More than we realized, right? Maintenance touches them a lot more than we think. So we started going after some of them and slowly, you know, obtaining some of those previous operators that have been out there for quite some time. So it’s just been a, a, a multi-front effort, on getting some of these guys the hands-on and the virtual reality and classroom training that they, they deserve.
– [Warren] Is that going to be a, a one-time thing or is that going to be an annual or semi-annual or…
– [Skipper] We’ve discussed like an annual type basis.
– [Warren] Annual?
– [Skipper] Yeah.
– [Warren] Just doing refreshers and everything?
– [Skipper] Absolutely.
– [Warren] All right, cool.
– [Hengst] What do you think the future steel mill’s going to look like, You know,
– [Skipper] Wow.
– [Hengst] 10, 15, 25 Years from now?
– [Ross] Well, automation, automation, automation.
– [Skipper] Yes.
– [Warren] If you look at it, historically across the board, right? You had an integrated mill, which is as big as a city, right? Literally it’s a city block, there or more. I, the one mill that I worked at for a while, it was, you pull in the contractor’s gate, it was almost two miles to get to the furnace area. So I mean, integrated mills were huge. And then in the late eighties, early nineties, you came into the, the mini mill, right? And, and, and that kind of shrunk that whole process down to where instead of employing, you know, 10,000 people, you had, you know, 500. To now you’re at a micro mill,
– [Skipper] Micros.
– [Warren] Yeah, and the micro mills, they’re very, very specific, very focused on producing just what they need out the door. Like I said, it, it’s smaller and smaller and smaller, but I think a lot of that has to do with what you just said, Chris, and that’s the automation and everything that is being improved upon as far as the equipment.
– [Ross] Yeah and AI is going to be huge. I mean, you look at some of the, you know, without getting any into, you know, really specifics, but there’s companies out there that, that tie in, I mean, everything, it’s like we were talking about with the, with the operational issues. I mean, they tie everything together. It’s, it’s going to become so op automated that… Obviously you can never do away with the people, right? You know, but it’s going to become very targeted, very specific. A lot of this stuff is, is, is machine learning. All these programs that are coming out now operational wise. I mean, you can go in, there’s a couple of shops I know now that we were kind of joking about, “If you guys lost your automation, could you still operate?” Do you have the people or the knowledge? Could you still operate? Typically the answer is, we probably could, but we’re not going to. You know?
– [Warren] Yeah.
– [Ross] It’s, it’s, and that’s a good thing. I mean, it’s from a safety factor, but also from an efficiency factor. I mean, it’s, it’s going to become, automation is just, that, That’s the way it’s, it’s going to be. And like Jim spoke to, a lot of these mills too are becoming, they’re very targeted in the, in the markets that they’re going after, product wise and logistics wise. They’re putting these mills in
– [Skipper] Yeah.
– [Ross] for specific reasons, specific locations and targeting certain markets.
– [Warren] How many, do you know how many acres EVRAZ has?
– [Skipper] Oh, I couldn’t tell you the acreage. That’s huge.
– [Warren] Oh yeah, it’s, it’s, it’s monstrous.
– [Skipper] Huge.
– [Warren] Do you know when it was, when was it started? Do you know?
– [Skipper] The, the mill itself?
– [Warren] Yeah.
– [Skipper] Oh man, I think we just celebrated our 150th anniversary.
– [Hengst] Wow.
– [Skipper] Last year.
– [Warren] So I mean, that’s a, the place is massive, right? So, that we were just talking about that earlier. Just, just the history that’s there, right? ‘Cause the one building, you know, thinking that Carnegie was there, right?
– [Skipper] Yeah.
– [Warren] Back in the day. It was just, like I said, that was just amazing.
– [Skipper] Sense of pride, I think, you know,
– [Warren] Yeah, yeah.
– [Skipper] being, you know,
– [Warren] Exactly
– [Skipper] involved with, with stuff like that. And, and that’s the reason why I’m still in the steel business, is, you know, the, the people that you meet, and the things that you’re around, and the, the projects that you get to be involved in are, are things that, you know, touch people, and touch families and, you know, could potentially touch generations,
– [Ross] Absolutely.
– [Skipper] when you really think about it.
– [Warren] Yeah. When I, when I, when I left the mill and, and went to the crane service company, you know, I, for years I had people asking me, well, you know, “I guess you don’t miss the mill?” And, and that was the thing, right? You really didn’t mi-, you miss the environment of the people, right? But, like I said, steel kind of gets in your blood a little bit. But like you just said, the, the people is what really drives that, that whole culture. It’s, it’s the get it done kind of attitude. Don’t, don’t, don’t mess with it, just fix it. Go, make steel. Like you said. It, it’s awesome.
– [Ross] Well, you know, well, I thought, we’ve all joked about it, steel industry itself, it’s this huge, massive industry, but the family’s really small.
– [Skipper] Yes.
– [Warren] Yeah.
– [Ross] It’s the same group of guys.
– [Skipper] Same guys.
– [Ross] You just, we rotate, right? I was on the steel side then I was on electrode side. Now I’m with Mazzella. And, and once you, and like Jim made a good point, you get a, you get it in your blood, and it’s, it’s addictive. You can’t get, it’s almost like you can’t get away from it because there’s never that, you never, the the cool part about these jobs too is, is to go see the latest and greatest technology that’s coming out. And then of course you, you have some facilities where you go back and, and it’s, you know, unfortunately they’re not upgraded yet. But, you can see comparisons and you get to look at everything but you still get to be a part of the steel industry. And that’s really, really cool.
– [Skipper] Pride.
– [Ross] It is pride.
– [Hengst] Thank you for joining. So be sure to visit EVRAZNA.com. That’s E V R A Z N A .com. And as always, you can get ahold of myself, Jim, Chris, or any of our other experts at mazzellacompanies.com. Don’t forget to pop into our learning center. We have a ton of information there. Subscribe to Safety Factor wherever you listen to your podcasts. You can also watch it on the lifting and Rigging channel on YouTube. My name’s Ben, stay safe out there.
Guests:
- Michael Skipper, General Supervisor of Rail Mill Operations at EVRAZ North America
- Jim Warren, Director of Steel Segment at Mazzella
- Chris Ross, Key Account Manager for Steel Sales at Mazzella
Background Reading:
- What is the No-Touch Electrode Handling System?
- No touch hand tools can help to reduce hand and finger injuries by facilitating safe movement of the load. How to Use No-Touch Hand Tools to Reduce Injuries on Your Job Site
- Are you looking for a more efficient way to rig a crane hook? Elebia evo Automatic Crane Hook: Design, Benefits, & Best Uses
- OSHA Hierarchy of Controls: Reducing Fall Hazards for Working at Height
Related Podcasts:
- How To Make Your Overhead Crane Safer
- How To Make Your Overhead Crane More Efficient
- How Is ITI Incorporating Technology Into Crane Operator Training?
- How To Start An In-House Safety Program
Learn More:
- About EVRAZ North America
- Mazzella Electrode Handling Solutions
- Follow Mazzella Companies on LinkedIn
- Subscribe to The Lifting & Rigging Channel on YouTube
- Subscribe to the Advancing Careers YouTube Channel
Contact Mazzella:
Schedule Remote or In-Person Rigging Training
Contact Mazzella’s Rigging Division
Subscribe wherever you listen!
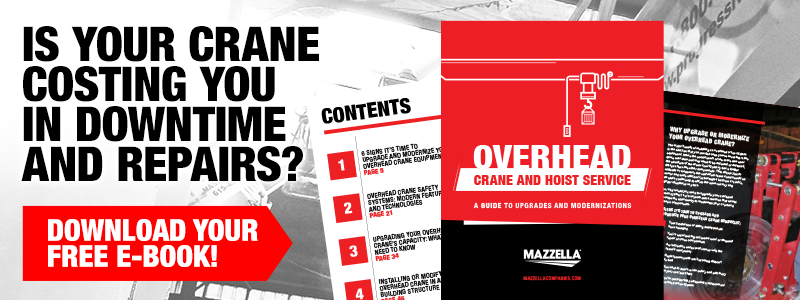
In This Podcast:
0:00 – Intro
1:04 – Meet some of the steel industry’s experts
2:13 – What are the biggest safety concerns in steel mills today?
3:05 – How can steel mills eliminate or mitigate hazards?
4:41 – How have safety procedures evolved over time?
6:25 – How has training for steel mill workers changed?
9:30 – How did the focus shift to safety in steel mills?
10:00 – How did data and analytics impact the safety focus?
11:23 – Why is safety now a point of pride in steel mills?
13:16 – What new technologies are improving safety?
15:46 – How do “no-touch” tools and smart features increase safety?
21:00 – How are training and cardinal rules helping improve safety?
24:27 – What barriers slow adoption of new safety technologies?
25:34 – What training procedures can be put in place to improve mill safety?
28:04 – How will automation shape the future of steel mills?
30:56 – How does the steel industry drive a culture of family and pride?
33:25 – How can you learn more?
Disclaimer:
Any advice, graphics, images, and/or information contained herein are presented for general educational and information purposes and to increase overall safety awareness. It is not intended to be legal, medical, or other expert advice or services, and should not be used in place of consultation with appropriate industry professionals. The information herein should not be considered exhaustive and the user should seek the advice of appropriate professionals.