Mitigating Risks in Steel Mills with Multi-Elevation Crane Safety Technologies
Emerging technologies aim to address safety challenges posed by utilizing multiple cranes at varying elevations in steel mills.
As steel mills operate cranes on multiple levels, collision risks contribute to ongoing safety issues. Now new automation solutions seek to mitigate these concerns through technologies like “no-fly zones,” positioning systems, and traffic management.
In this episode of the Safety Factor podcast, we explore the current state and future potential of multi-elevation crane safety. Industry veterans detail technologies developed to prevent accidents, boost productivity, enhance training, and more in steel mill settings. Discover insights from decades of crane modernization experience.
Hear perspectives on balancing safety advancements with costs considerations. The guests offer predictions for smarter cranes and infrastructure changes on the horizon. From warnings when entering hazardous areas to controls preventing contact, innovations remove workers from harm’s way. Though equipment continues advancing rapidly, experienced oversight endures throughout steel’s automation evolution.
The steel industry has predominantly been a little bit behind the technology curve, and really, we should be leading the curve. Because this is one of the most expensive downtime-related industries.
Mark Shubel, Mazzella Director of Crane Service Technical Training & Applications
- Learn how multi-elevation cranes function in steel mills and heighten risks
- Discover technologies like “no-fly zones” to avoid collisions
- Hear how automation improves productivity and eliminates distractions
- Get perspectives on justifying costs with injury/downtime prevention
- Find out where industry experts see continued crane safety advances heading
If you want the inside look at the future of multi-elevation crane safety, don’t miss this Safety Factor episode!
Transcript
Is the Steel Industry slower to adapt to new technology?
[Mark Shubel] You know, yesterday we were in the AIST meeting, and they made the comment that, you know, we’re behind the times in technology, and integrating technology.
[Steven Lubeck] Oh, don’t worry, I got nominated, so don’t worry, I’m going to take care of that.
[Shubel] Yeah, I know. Hey.
[Kenny Wright] You weren’t there.
[Lubeck] I wasn’t there.
[Shubel] Yeah, I voted for ya.
[Wright] But the comment was made that end users are behind. It isn’t the people like us that are pushing the technology…
[Shubel] No, no, no. Well, I was wondering if we should make a comment about that, that in essence, the steel industry has predominantly been a little bit behind the technology curve, and really, we should be leading the curve.
[Wright] Yeah, we should.
[Shubel] Because this is one of the most expensive downtime-related industries,
[Wright] Agree.
[Shubel] and they should be going, “Why are we five years behind? When we should be three years ahead of everyone else.” So it really comes down to the end users, the mills and stuff, recognizing that this is valuable. So I don’t know how to put that into words, but…
[Ben Hengst] You just did.
[Wright] So the end users, over the years, have been reluctant to change.
[Shubel] You didn’t record it, so we’re screwed.
[Hengst] I’m still recording.
[Shubel] ‘Cause I can’t repeat anything I ever say, ’cause it’s unscripted.
[Hengst] I caught it. Yeah, we’re good, I’m still recording.
[Shubel] I don’t know, is that something that’s worth talking about?
[Lubeck] Yeah.
[Shubel] Okay.
[Wright] And I don’t think we just pick on the steel industry, we got others that are in the same boat. Automotive, everybody could learn from automotive, ’cause their overhead cranes now have all the features you could ever imagine on ’em. Tier one, tier two suppliers, but I think that’s a whole ‘nother segment. Sorry, we get a little bit excited about this stuff, so…
[Hengst] It’s perfect.
[Lubeck] It’s funny, because, like, on this… The one crane we did, the dual-elevation crane, obviously for commissioning. I saw their cranes cross, and then I saw ’em stop, I’m like, “Wow.” And I’m like… It’s like watching paint dry, you know? And I’m like, “Whoa, the hook’s down, they stopped. Cool.”
[Shubel] You’re like, “It did what it was supposed to, isn’t it cool?”
[Lubeck] It worked perfectly.
[Shubel] Yeah, I know.
[Lubeck] You know? I don’t know, it sounds kind of stupid, right?
[Wright] You’re not really shocked that it worked properly though, but you’re like, “Oh, thank goodness.”
[Lubeck] Yes.
[Shubel] Well, you’re excited because that’s what your goal was, and it’s the same thing when we install cranes, or build them and install ’em and see ’em work. You’re like, “That’s so cool.” And you’re… And to your point, Kenny, you go, “God, it’s actually working.” Now, you knew it should, because you did all the leg work up front, but when you actually see it, there’s a huge sense of accomplishment.
[Wright] There is.
[Shubel] And you go, “Damn it, I helped with that. That was so cool.”
[Wright] I agree.
Intro
[Announcer] For your own safety, you are reminded to stand behind the yellow line.
[Hengst] Welcome to “Safety Factor”, my name is Ben Hengst, and today we’re talking about the future of multi-elevation crane safety in the steel industry. I’m joined once again by president of Laser-View Technologies, Steven Lubeck. As well as Mazzella’s crane experts Kenny Wright and Mark Shubel. So, could you guys introduce yourself a bit? Tell us a bit about your background in the industry?
Who are the overhead crane experts?
[Wright] Alright, so my name’s Kenny Wright. I’m the VP of our mods and process equipment group. My background, I’ve been in the crane industry for about 30 years. Training-wise, education-wise, I have an electrical and electronics degree. And my goal when I got into this world was to be an automation engineer, but Mr. Shubel convinced me to work on cranes instead, and we’ve had a lot of success and fun over the years.
[Lubeck] So my name is Steve Lubeck, I’m with Laser-View Technologies. I started a company back in 1999. But formally, I actually am a mechanical engineer by training, and I learned controls, and everything else that goes along with it. More recently, we have been involved with sensors, and dealing with automation. Sensors then evolved into putting sensors on cranes, and bringing cranes into the new era, and I’ve been doing that ever since, and having fun with that.
[Shubel] My name is Mark Shubel, I’m the director of business development and technical training at the Mazzella Companies. I’ve been in the overhead crane business for the last 36 years. Before that, I was involved in automation robotics. And my background’s in mechanical and structural engineering.
What are multi-elevation overhead cranes?
[Hengst] Okay, so today, we’re talking about multi-elevation cranes, so I guess the first question is, “What are they?”
[Wright] So, multi-level cranes… When you have one runway, it’s possible to have multiple cranes on that same runway. So, in that bay, you could have another crane at a lower elevation, a lower runway, and/or it could be a semi gantry, or a gantry crane that’s also in that bay. Those cranes could come into contact with each other, they could collide. And so, that’s what multi-level cranes are.
How are multi-level overhead cranes used in the steel industry?
[Hengst] So how are they used in the steel industry?
[Wright] When you say, “How are they used in the steel industry?” Like, an example would be, like, in a rolling mill, where you have the overhead cranes that are taking care of certain parts of the rolling mill and the steel mill. Then you would have a jib, or a gantry crane, or a semi gantry crane that’s on the other end, where the output is, that are handling, like, discrete plate, or certain types of plate that they may be running.
[Lubeck] Well, in other cases I’ve seen it also where the upper runways only go a section of the building, and the lower… Or usually the whole building. And the lower runways only go maybe half the building, or two-thirds of the building. So, sometimes you need to get material from one place to another place. So the upper crane takes the material, drops it off near the end of the runway, and the lower crane can then take that. So the runways then cohabitate in a certain area. And oftentimes, what happens is, is that you want to keep those cranes from cohabitating the same area at the same time. So you have… You want to keep one crane out while the other crane’s in, and the other crane when the other crane’s in.
What are the safety risks associated with multi-elevation overhead cranes?
[Hengst] So what is some of the safety risks associated with multi-elevation cranes, besides just collision?
[Shubel] Well, there are obviously numerous safety concerns when you have that situation occur. And always the operators in danger at those types of things. And not only is the operator in danger, but also equipment damage and loss of production. So it’s always been, in the past, something that the individual operators had to contend with, without the technology to help support that effort. And with that regard, sometimes, if you get operators that are distracted, you have incidents occur, and equipment’s damaged, or people are injured, or… You know, or worse, and so, obviously, the industry has been looking for years to advance themselves so that they’re a lot safer and a lot more efficient in these types of endeavors, and that’s one of the things that Steve and his company does, and Mazzella, as an integrator, focuses on. Looking at new technologies to bring ’em into the industry, to make a safer, more productive workforce with less damage to equipment and processes, and people.
[Wright] So… And most of our customers have, like, a written process, right? They have guidelines for their operators, they have, you know, certain warning devices that they may employ throughout the plant. But, I mean, they do have a written process for this, but operators get distracted. I mean, they do. Things happen, cranes break down, and you know, they don’t… No longer have their safety features involved. So… Just wanted to add that though, that most our customers do have…
[Shubel] Yes, they do.
[Wright] A written process.
What challenges are there when operating dual-elevation overhead cranes?
[Lubeck] But the thing is, is a lot… In the dual-elevation cranes I’ve seen, they tend to be higher elevation. So instead of being a 30-foot-tall crane, they’re hundred-foot-tall cranes, because of the nature of the buildings they’re in. And when you have two cranes, one a hundred-foot, maybe the other 75-foot or 80-foot, and you’re looking at an angle from the ground, you may get fooled by their perspectives. So basically, you think you’re clearing, but you may not clear. And a lot of these cranes also have a main hoist and an aux hoist. Well, if the main hoist or the aux hoist is a little bit too low, and not tucked up into the nest, that hook… The hook… Well, it can grab a festoon, grab a railing… I have a customer that’s done it multiple times over the past 10 years. Grab festoons off a lower crane, railings, controls, let alone, almost pull a crane off a rail, because, you know, you’re pulling a lower crane off. So, although it’s obvious that you don’t want to do that, when they’re crossing and you’re on the ground, it looks like they’re about to hit, but there’s clearance there, you just have to have your hooks all the way up.
How can you mitigate the risks of collision between multi-elevation overhead cranes?
[Hengst] So, how can you mitigate some of those safety concerns?
[Wright] So, one thing that’s important for the operators, is that they should always maintain the control of the crane that they’re running, right? You don’t necessarily rely on the electronics or any safety feature, or anything that’s installed on that crane, to 100% mitigate any of the risk. The operator is still responsible. But if we have certain devices, and I know Steve and Mark will touch on that, is if you have certain features, certain devices installed on the crane to keep them from colliding, or keep them out of the same bay, such as zone control, you give the operator a little more trust in the equipment, that he’s not going to be solely responsible for something that could go wrong, right?
Mitigating risks for dual-elevation overhead cranes that use the full span of the runway
[Lubeck] So, there’s kind of two compartmentalized topics here. The dual-elevation crane, where you have two large cranes that are an entire span, lower and upper. That’s one situation. And then you have the situation with the gantries, where the lower crane is half the span, or a third of the span, where you can get around it. Talk about the first application, right? Where you have the full-span cranes? It’s a key that you have a hoist upper-limit switch. So you have to know whether the hoist is all the way up. And you can train the operators that they raise their hoist to the upper-limit switch, all the way, before they move a crane underneath, or they move a crane over top. Well, that’s the first thing. But if they don’t actually go to the… Cause they don’t want to take the time, to go to the upper limit, that’s when you have the problem. So, one way that we’ve gotten around that, is we have inputs that tell me that hoist upper-limit switch is met, for sure, on both hoists. And then, you actually know where the cranes are. You have lasers that position the crane the whole length of the runway. You do the same for the lower cranes. It’s basically like a traffic cop. So, I know where the top cranes are, I know where the bottom cranes are, I know whether the hoist is all the way up. I know how close it can come. And I know that you can’t lower on top of another crane off-side. So you have a traffic cop, and if the traffic cop system’s not operating, none of their cranes work. They all have to work in conjunction.
Mitigating risks for dual-elevation overhead cranes that use a partial span of the runway
[Hengst] And what about with the gantry cranes?
[Lubeck] So, the gantry cranes are kind of the same, but a little different beast. They get a little more complicated. So, the same holds for gantry cranes, but oftentimes, I’ve found with gantry cranes, people want the trolley to be off to the side, to pass around the gantry. And then… Instead of going over top of it. If you have enough headroom, you can go all the way up. But then, you have to look at the rigging. So, in the case of a gantry crane, oftentimes, you want to make sure that the overhead crane goes around it. And sometimes, when the hoist is all the way up, people will say it’s okay to go over top of the gantry. And the big thing with gantry cranes, the challenge there, is I’ve heard people that flip over multiple gantries, they’ll take the overhead crane, snag it, and they’ll literally pull a gantry over, believe it or not. But if you have rigging on the gantry, slings, you’re always going to snag it, no matter what. So it depends on what you do. If you have rigging on there, you can never go over top, if you don’t have rigging on there, sometimes it’s permissible to go over top. But that’s where a no-fly zone takes place then, a two-axel no-fly zone.
What are “no-fly zones” for overhead cranes?
[Hengst] So can you explain a bit about what no-fly zones are?
[Wright] So we set up zones where an overhead crane can pass over or around other equipment. It doesn’t have to just be a crane, by the way, when you were saying that.
[Lubeck] Right, right.
[Wright] It could be machinery of any type that the overhead crane, if it has rigging on it, if it has a spreader bar on it, that it would collide with the machinery. No-fly zone is, that area where the crane definitely has to have it’s hoist in a certain position, it’s trolley in a certain position, before it can travel over that work area. And it can work in reverse too, you could set up no-fly zone for the gantry, or a semi gantry, if it’s in the same bay as an overhead crane. Alright? The semi gantry or gantry cannot travel beyond column line C if the overhead is working in that area, so it could go both ways. It’s not just a… The device, not just on the overhead crane, it’s on the gantry crane as well. Another example of a no-fly zone is such… steel mills. You have the operator’s pulpit that is on the operator’s flooring, right? We can set up no-fly zones for the crane, whether it has attachments on it or not, that it can’t get close to the pulpit if the hoist is in a certain position, or the trolley’s in a certain position. Did I do good on that?
[Lubeck] Good on that. I mean, I’ve seen situations where pulpits have been in that plant for 10 years, and someone new is there, and they’ve run a coil through a pulpit. So, it’s happened, and no-fly zones will keep those things from happening, if someone is not paying attention as much.
How sensors on lower and upper overhead cranes force safe operations
[Lubeck] But, what I want to add to the gantry crane topic was… Is that, oftentimes, people have policies where, if you have a small gantry crane, or I call work-station cranes, oftentimes in the bay. You take the work-station crane or the gantry crane, and you move it to the end stop, and then you’re allowed to bring the overhead over top. Well, that doesn’t always happen. So let’s say that that process is still a good process by putting assessors on the lower crane and having a system on the upper crane, you can force that they have to have that gantry at the end of the runway in order for the overhead to go over top. Or you compartmentalize it, you can break the gantry area into sections, or you can make it dynamic, so you can follow each other. Lots of things that you can do. And the best way of doing this is, we do wireless IO between the upper crane and the lower crane, and everything is all synced together.
[Wright] And it’s really up to the people installing it, and the people commissioning it, as to the limitations of what the components can do, right? I mean, would you say that, both of you? It’s like…
[Shubel] Yes.
[Wright] Whatever you can imagine, Ben, it’s… You can set those zones up to be whatever you want ’em to be. So…
How training helps overhead crane operators understand how the new technologies function
[Shubel] Kenny touched on a very important point earlier too, is that, it really all starts with operator, and operator training. And so, what we’ve seen in the industry just in the last few years, there’s been greater emphasis put on operator training than ever before. Because we realize that, in order to mitigate the risk for injuries and equipment damage, that it has to be a… Kind of a multi-pronged approach. So the technology works great, and it does what it needs to do, and it’s continually evolving, but really it comes down to the operators not only understanding what they’re doing and being trained properly, but also understanding the technology that they’re working with, so that they can relate to how that works also. So again, it’s kind of a multi-pronged approach. And in order to be very successful with this, even when we install new systems like Steve offers, one of the very important things for us to do is to train the operators so that they understand what we’ve done to the equipment in order to make it more safe, so that they understand, when they’re using the equipment, why it reacts in certain ways. So again, it’s kind of a dual-type of a role that we need to address, not just the technology, but also the operator training, so that the operator understands what’s happening with the equipment when it comes into these modes, like Steve’s able to offer, where it has slowdown modes, or stop modes, things like that, so they don’t think the equipment’s malfunctioning, they go, “I’m in one of the zones that I have to be careful at.” And then they pay a little more attention to what they’re doing.
[Hengst] And really if they’re… If it’s not working properly, then that means that they’re doing something that they should not be doing.
[Lubeck] In some cases, yes.
[Shubel] In most cases, yes. Very seldom does the technology fail now, I mean, just like all of the emerging technologies, when they first come out there, there are some bugs in ’em occasionally. But these have been proven and shown to be reliable now, and just… You know, for years and years, and in literally thousands of cases. So the technology’s advanced far enough ahead where, you know, the incidents of the equipment failing from a technology standpoint, doesn’t really impact the equation that much. And then, again, when it does fail, it usually shuts something down, which stops them from using the operation, so, in essence, even when it does fail, it doesn’t allow them to do damage to themselves or the equipment.
[Lubeck] Yeah, we try to… It’s best to design the systems as much fail-safe as possible. And the word “fail-safe” doesn’t mean that… Redundancy, it means that when you fail, you fail in a manner such that you can’t let the operator keep operating the crane. And until they override it, they acknowledge it, maintenance knows it, and everyone knows that, that feature has been turned off temporarily so they can operate the crane.
How does overhead crane technology improve productivity alongside safety?
[Lubeck] The point I wanted to make also is, not just the training for the safety, but it adds productivity. And this is the piece that I have talked to people about, that they don’t really realize. Because, by putting these systems in, you actually change behavior. So when the operators know they always have to move the crane to the side, for the overhead crane to come in, they don’t waste time anymore. They don’t leave it here, move the crane, realize they can’t move it, and have to go move this crane. Their behavior changes, so now, they start moving the crane ahead of time, get the other crane, move their load, and they save time in material handling. And they’re not as worried about where they’re going. You know, they don’t jog the crane as much. They watch where they’re going. And look at the material movements and less worrying about, “Am I going to hit this, am I’m going to hit this? Is a crane in the way?”
[Wright] So when we teach operator training classes, at least I know Mark Shubel and I do, is that one of the comments we make to the operators is, “Your movements should be precise. They don’t necessarily have to be fast.” Right? And we’ve trained operators, everything from Goliath gantry cranes, rubber-tire gantry cranes, overhead cranes, overhead cranes with a cab, without a cab… And we always make that comment to ’em, it’s like, “It’s not the speed you’re looking for, it’s the precise movements.” And like Steve mentioned, if you can learn to use the equipment, the no-fly zone equipment, and know where those zones are at, then you make your precise movements, you actually are going to be faster. Production’s going to increase. Safety definitely is going to love us, because we’re not going to have any more incidents or accidents.
What extra features can be added to help crane operators?
[Lubeck] And we haven’t put lights… We can also do other things like light indicators, buzzers, lights on certain zones so that you know you’re there or you’re not there. So the things we can do to help the operator know it’s not a broken crane, it’s that he’s actually done something that… To switch a light, switch a mode. But sometimes, people don’t want the crane to stop. When you go over top of the gantry, they just want it to slow down. So sometimes, you want to make a slow aisle, or you’ll make a slow area. Or they just want to give a warning. They don’t want to stop the crane, but they want to do a warning. And all that’s very possible, it’s the same action that does it, really.
[Wright] And there’s no right or wrong to that. I mean, that’s what the end user wants, and that’s what the operators are asking for. And yeah, we can deliver that. Our preference is to slow down or stop the crane, I can tell you that. But, you know, we will work with the audible and visual alarms.
[Lubeck] Yeah, of course, of course.
How to understand what technology is best for your overhead crane?
[Hengst] So how do you balance…? So you said that, you know, you can do anything you want to the crane, like, you can put a ton of stuff on there. I assume that gets pretty expensive, so how do you balance the need for productivity and efficiency with the need for safety?
[Wright] So, on every instance of people asking for help for a situation that they have, we evaluate it, and we determine what components that need to be installed. And again, when I said it’s unlimited, it’s whatever you can think of to set up within the parameters of the operation that they have, okay? We can’t make the crane, you know, float in midair… And do things that… You know, that aren’t natural. But, it is really unlimited on how we can set up the zones, within a certain reason, I mean, you do have data that’s going to consume memory and the devices, so, I mean, there are certain limitations, yeah, but honestly, whatever you can think of, you can come up with. But back to your question, we assess it with the customer, “What are you looking for? What do you need help with?” We propose the components that we think will work for ’em, and then we present that to them. Then we start the back and forth on how the owner or end user wants it to really work.
[Lubeck] You know, oftentimes you’ll have a no-fly zone. It’s, “I want a no fly zone.” And my next question is, “Do you ever need to access that zone?” Oftentimes, the answer is yes. “Alright, how often do you do that?” “Well, once every month, once a year, once every three months…” You have options to how to access it. You can do it from a phone or a tablet, if it’s the right system, and hit a master override, turn a zone off. Then you have a key switch on the wall, with wireless-to-wall, that puts in a bypass. So it can go up on the crane, and they can jumper, or bypass it, or… Lots of ways, so it’s good to know how they plan to use it from a maintenance standpoint, how often. And what control, who gets control of making changes, bypasses, and all that. So that’s really important to know. And that’s a question we get asked often. If it’s a building or a pulpit, yeah, usually you don’t have to go over the top of it. If it’s a roll stand, they’ll have to go over top to pull rolls out. If it’s a CNC machine, a burning table, they’re going to have to go to do that.
[Shubel] One of the other things to think about in… You know, how is it cost effective for the customer, and when you present this to the customer, is really, “What does it cost not to do something like this?” So what is the cost of an injury to workers, or damage to equipment? A lot of our companies that we work with, obviously, out in the industry, they are production-related type companies, and the equipment, we call ’em process-related equipment, in that, in order for the building to be able to create the product that they’re producing, the cranes have to be operable pretty much a hundred percent of the time. And cost of downtime for even smaller plants that aren’t involved in heavy processes, is sometimes in the tens of thousands of dollars per hour. Some of our customers have cost upwards of a million dollars an hour. So when we talk about some of these systems, and by the way, they’ve gotten really, very competitively-priced, I think, right now. But, when we talk about the cost of this, this is basically a drop in the bucket. I think OSHA has indicated that, sometimes the cost of an injury right now is somewhere in the neighborhood of around $300,000-to-400,000 to an individual, when you talk about all the lost time of work, and the incident itself, and whatever needs to be done from a… Maybe a first-aid or hospitalization thing. And so, when you look at the cost of doing this for tens of thousands of dollars, versus the cost of hundreds of thousands of dollars if a person gets hurt, or possibly millions of dollars if a plant’s shut down for a day, or two days, It’s very easy for an end user to go, “Where do I spend my money?” I spend my money in prevention, not in the aftermath of it.”
How does overhead crane technology help improve uptime in the steel industry?
[Hengst] Where do you see the future of the technology going? What do you…? Let’s talk specifically about steel mills. Where do you see the future…? A future steel mill, how does it look?
[Lubeck] Well, I think steel mills are looking at the safety mainly, I think. I think that’s a big piece of it. There’s so much noise going on, there’s so much other distractions. And there are so many cranes in a mill, moving on the same runway. So I think that’s why the steel mills are looking more for safety. But, there’s also other parts of it. You know, when you do have an incident, and you snag a wire rope, that wire rope now needs an inspection. So if I snag the rope… Typically… Am I correct?
[Wright] No, you’re correct.
[Lubeck] On… Against another crane. If it’s reported, you’re supposed to now inspect it and make sure you don’t have broken strands, or anything like that. So, I see the steel industry looking for uptime. And this is an inexpensive way of securing uptime, and waiting through the maintenance on scheduled, you know, outages. The other thing is, is that the systems are more than just isolated islands now. The system that’ll keep the upper cranes and the lower cranes monitored, can also have remote monitoring on them now. So, we can equip these with remote monitoring that literally… We could see anywhere in the world. Now, granted, you can’t fix all problems virtually, right? Wiring, you probably can’t fix virtually. But I can lead to where a wiring problem is. So, you can get the safety system, or the production system up a little faster, by knowing that a laser sensor might have gone out, a cable may have gone out, or simply, someone reset a parameter wrong. So there are lots of ways of keeping the uptime on these systems, and one argument I think people do make still, is that by doing this, potentially, what happens if something breaks? And that’s one way of alleviating that.
[Wright] But if the electronics do fail, you do have a way to put it in a bypass mode and continue operation.
[Lubeck] Correct.
[Wright] Until you can get up, look at it, work on it and get it repaired.
What does the future hold for overhead cranes in steel mills?
[Wright] The same thing that Steve was saying, I see that cranes in the steel-mill world are becoming more and more advanced electrically and electronically, okay? It’s just going to happen. You have a younger generation of guys coming along that are going to be running these mills, running these overhead cranes, you know, working in and around all the equipment, and they’re used to the electronics, they’re used to the driverless cars, if you want to call ’em driverless, you know, sitting in a passenger seat and take a nap while it takes me to work, you know? They’re used to the electronics. The older guys too, they’ve adapted very well to the electronics. They all want one thing, they want it to be safe. They want it to be reliable, and they don’t want the headache of it breaking down intermittently, and the hassle of it breaking down intermittently, okay? So the components are reliable, they do work, and they do provide a feature to the operators that makes them more safe. And that’s… At the end of the day, everybody gets to go home. That’s all everybody wants.
[Lubeck] And one other comment to that, is that the systems that we’re building now, we’re building with looking into the future, so that we make them so that we can add things later. So we keep developing new things that will add to safety other than no-fly zones. So potentially, we try to make the systems now, so later, we can do other preventative measures. And build it into the same systems, report back mechanical issues and monitoring and things like that, and add it to all systems. Is it there now? No. But the platform is there, that we can add things later to keep advancing the mills.
Advice for finding companies that can integrate technology on overhead cranes
[Shubel] And that’s really… When you start getting into systems integrators like ourselves and companies like Steve’s, that’s one of the really key foundational issues, is that this thing is scalable, and it creates a good base foundation. The technology’s always continually going to improve, just like computers have, and televisions, and everything else. So, once we get people interested in this type of technology, they’re more, I guess, understanding about changes in the technology, and new emerging technologies, and they start asking for those types of things to make their plant more productive and more safe. And to Steve’s point, having something that you can build on, a platform that you can build on and expand on, it’s very important. So when you look at companies to do these types of things, make sure you look at a company that does that, and keeps that in mind, so that, when you do have to invest in the future, you’re not wasting the money you spent initially. It’s something that can still be used, although it may be modified. So, for instance, in Steve’s case, you know, the controls and the sensors that are currently being used five years from now obviously will be obsolete. But that doesn’t mean the system itself is obsolete, or the components that are used, all of the components…
[Lubeck] There’ll be a path forward.
[Shubel] Just certain things will be updated. And that’s kind of very important to consider, when you’re looking at making this type of an investment.
[Lubeck] Yeah. There’ll be a path forward. The other comment I have, is that going forward in the future, I think the protocols are used to communicate with the systems are changing. You know, the standard now on most cranes new or retrofitted is, you have dry contacts to the enable input, so, for example, on VFD, or between the radio and the VFD. Well, as newer cranes are coming in now, now they’re using the Ethernet IP… PROFINET Different protocols. And by doing that, you actually improve reliability, because you’re not dealing with clicky-clicky contactors all over. Now you do it with digital. And if you rely on a contactor as a secondary cutout, and use digital as a primary. So I think, going forward, things are going to change in that way, and have more… You know, less things to go wrong, more maintainability.
[Wright] Yeah. So the motor control electronics that are now onboard is… What he’s getting at, is so much more advanced than it has been in the last, even 15 years. And we are doing… A particular job that we’re doing right now for a customer, Steve’s involved in this one, is, everything is over Ethernet IP, everything. And the control room is actually 300 feet away from where the crane is at. And then the controls for the crane are 300-foot the other way, and everything’s over Ethernet IP, and makes our festoon packages smaller. In our opinion, it makes it safer. We can build in fail-safes within the coding. And then, the customer’s happy to, because he don’t have to go up on the crane if the controls are having an issue, because it’s either in the pulpit, or it’s in the MCC. He doesn’t have to go up there anymore.
[Lubeck] And the install time’s less, so there’s less wires to pull.
[Hengst] Which everybody loves,
[Lubeck] Which means less connections to go, less connections to loosen, less cables to break…
[Wright] More uptime, more reliability, so…
[Lubeck] So I think the… From that standpoint, Ethernet IP and… PROFINET Have been around for a while, but the standard is, I put a normal VFD drive on something. And that’s always been the standard, and now, slowly, people are realizing that protocols are acceptable.
How can you learn more about overhead crane technologies?
[Hengst] Alright, thanks, Steve. So be sure to visit laser-view.com. That’s laser-dash-view.com, and as always, you can get ahold of myself, Mark, Kenny, or any of our other experts at mazzellacompanies.com. Don’t forget to pop into our learning center, we have a ton of information there. You can also watch “Safety Factor” on “The Lifting & Rigging Channel” on YouTube, or subscribe wherever you listen to your podcasts. Thanks for listening, and stay safe out there.
Guests:
- Steven Lubeck, President of Laser-View Technologies
- Kenny Wright, Vice President of Process Cranes and Modernizations at Mazzella
- Mark Shubel, Director of Crane Service Technical Training & Applications at Mazzella
Background Reading:
- How Can Collision Avoidance Systems Improve Jobsite Safety? How Do Collision Avoidance Systems Make Overhead Lifts Safer?
- With modern technologies becoming more readily available and more affordable, the safety features available for overhead crane systems have never been better. Overhead Crane Safety Systems: Modern Features and Technologies
- Many employers don’t understand who is responsible for providing training for employees who operate overhead crane equipment. Crane Operator Training: Who’s Responsible for Training Your Employees?
- How Does the No Touch® Electrode Handling System Make Steel Mills Safer?
- Keep Workers Safe With Elebia Automatic Hooks for Steel Mill Rigging
- What Technological Advancements Have Made Lifting and Rigging Safer? How Is Technology Changing the Lifting and Rigging Industry?
FREE Downloads:
- Overhead Crane & Hoist Service E-Book: A Guide to Upgrades & Modernization
- Overhead Cranes E-Book: Overhead Cranes From Top To Bottom
- Lifting & Rigging Site Assessment Guide
- Lifting & Rigging Best Practices Infographic
- Overhead Crane / Hoist Operator Daily Inspection Checklist
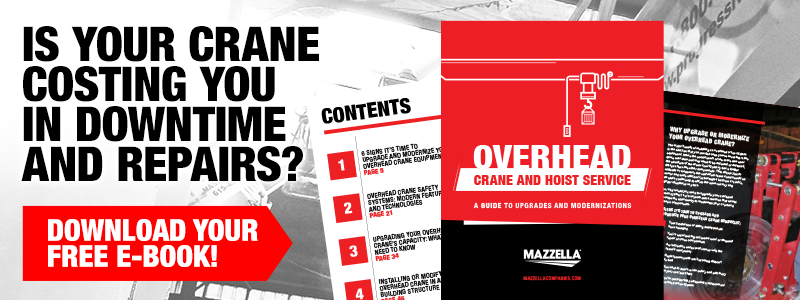
Related Podcasts:
- Steel’s Sprint From the Safety Stone Age
- How To Make Your Overhead Crane Safer
- How To Make Your Overhead Crane More Efficient
- Overhead Cranes 2.0: How Automation is Revolutionizing Crane Safety
- How Virtual Reality and Augmented Reality Are Revolutionizing Industrial Training
Contact Mazzella:
Schedule Remote or In-Person Rigging Training
Contact Mazzella’s Overhead Crane Division
Subscribe wherever you listen!
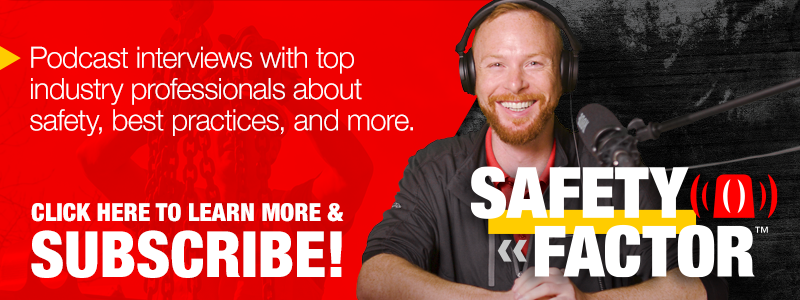
In This Podcast:
0:00 – Is the Steel Industry slower to adapt to technology?
2:28 – Intro
3:05 – Who are the crane experts?
4:24 – What are multi-elevation cranes?
4:57 – How are multi-level cranes used in the steel industry?
6:02 – What are the safety risks associated with multi-elevation cranes?
7:39 – What challenges are there when operating dual-elevation cranes?
8:53 – How can you mitigate the risks of collision?
9:42 – Mitigating risks for dual-elevation cranes using full runway span
11:18 – Mitigating risks for dual-elevation cranes with partial runway span
12:30 – What are no-fly zones for cranes?
14:10 – How sensors on lower and upper cranes force safe operations
15:21 – How training helps operators understand the technologies function
18:11 – How does the technology improve productivity alongside safety?
19:55 – What features can be added to help crane operators?
20:47 – How to understand what is best for your crane?
24:52 – How does this technology improve uptime?
27:04 – What does the future hold for cranes in steel mills?
28:51 – Advice for finding companies that can integrate tech on cranes
32:35 – How can you learn more about crane technologies?
Disclaimer:
Any advice, graphics, images, and/or information contained herein are presented for general educational and information purposes and to increase overall safety awareness. It is not intended to be legal, medical, or other expert advice or services, and should not be used in place of consultation with appropriate industry professionals. The information herein should not be considered exhaustive and the user should seek the advice of appropriate professionals.